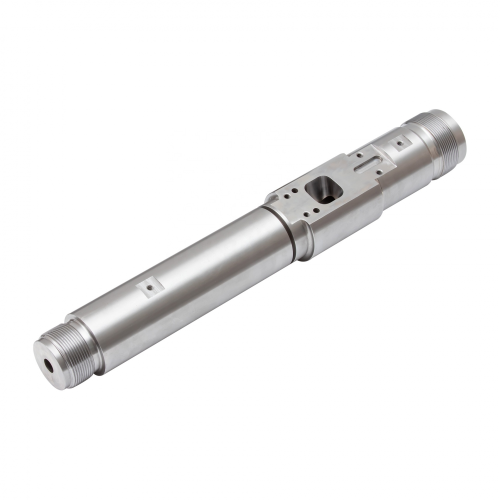
injection molding screw shenzhen
-
$6.00≥10 Piece/Pieces
- Min. Order:
- 10 Piece/Pieces
- Min. Order:
- 10 Piece/Pieces
- Transportation:
- Ocean, Land, Air
- Port:
- ShenZhen
Your message must be between 20 to 2000 characters
Contact NowPlace of Origin: | China |
---|---|
Productivity: | 10000 |
Supply Ability: | 8000000 |
Payment Type: | L/C,T/T,D/P,Paypal |
Incoterm: | FOB,CFR,CIF,EXW,FCA,CPT,CIP |
Certificate: | IOS9001 |
HS Code: | Non |
Transportation: | Ocean,Land,Air |
Port: | ShenZhen |
THE OBSERVED DIFFERENCES BETWEEN PLASTICS PROCESSING IN EXTRUSION AND INJECTION MOLDING
Quality Control - Plastics processing requirements in injection molding are similar to the requirements in the extrusion industry. Many of the terms are different; for example, rate in extrusion is defined as pph/rpm, and in injection oz/sec. The primary difference is of course extrusion is continuous and injection is start - stop.
Extrudate quality in extrusion is easier to monitor than in injection as it is continuous. Extrusion systems normally accurately monitor melt pressure, melt temperature, and amps. The end product is normally continuously measured in thousandths of an inch or better. With this type of continuous monitoring quality problems are quickly addressed.
Extrudate quality in injection molding is normally only considered when obvious part discrepancies occur. Examples are: color streaking or mixing, recovery times that increase cycle times, melt temperatures that either are to low, when coupled with inadequate injection pressures, will not allow the mold to be filled (short shot), or conversely to high, causing part flash or mold drool.
The reasons for this lack of proper extrudate quality monitoring is twofold:
First - most of the parts that are molded are initially designed to use a specific resin with adequate physical properties. Parts are then tested and finally placed into production. The actual molding may be placed in a machine that has inadequate inject pressure. In this example to overcome the lack of adequate inject pressure, the setup man increases back-pressure and barrel temperatures to fill out the mold. Rarely will he check to see if the melt temperature is too high - his job is to fill the mold and make parts - he probably does not know that damage may be occurring to the resin due to increased shear or elevated temperatures. After the part is placed into production, physical testing usually only happens if failure occurs.
Second - Injection Molding Machinery manufacturing companies have not been required by molders to improve process technology primarily because the molder is not aware of the need for an advanced level of process technology or the advantages derived from improved process technology. Very few process technologists have made the transition from extrusion to injection molding. The ones that have rarely have had the opportunity to work in a "hands on" production molding facility.
Obvious hardware differences between Extrusion and Injection:
(1) L/D - Length divided by diameter (screw or barrel length /barrel inside dia. or screw outside dia.) in extrusion is normally 30:1 or greater; in injection molding 20:1 is still the normal l/d. The l/d in injection is further reduced as the screw reciprocates. The amount of effective screw length loss is in direct relation to shot size. Therefore the greater the shot size, the greater the starvation of resin due to the resin inlet being translated downstream in relation to the first feed flight. Injection screw designs normally have additional turns of feed section to compensate for this starvation.
Barrel and screw lengths in extrusion have constantly increased from 20:1(introduced in 1950) to 30:1 plus (introduced in 1960). The reason for this increased length is described in the formulas for rate and pressure flow.
Rate in cubic inches per second = (Q total = Q drag + Q pressure - Q leakage)
Pressure flow = Qp = p D h3 P sin2 f / 12 u L
Note the "L" variable is linear and the "h" variable is cubic in the pressure flow equation. This means any increase in depth must have a corresponding increase in length, or the pressure flow value will increase reducing total flow. This formula does not take heat transfer and melting into account, it is simplified to show only values for constant viscosity.
Why Choose Bergek
professional custom CNC Machining Parts Manufacturer in China
* Guangdong Aluminum Application Precision Technology Co, Ltd was established in 2012 and has over 10 years experience of in researching. developing and manufacturing CNC Machining Parts
* We have the recognition of famous brand customers all over the world
* Our company has more than 200 professional employees and over 10000 sqm modern factory area
* Our products own many patents and quality system certifications ISO 9001
* Our products own many patents and quality system certifications ISO 9001 is over 250,000 tons, exported to over 120 countries.