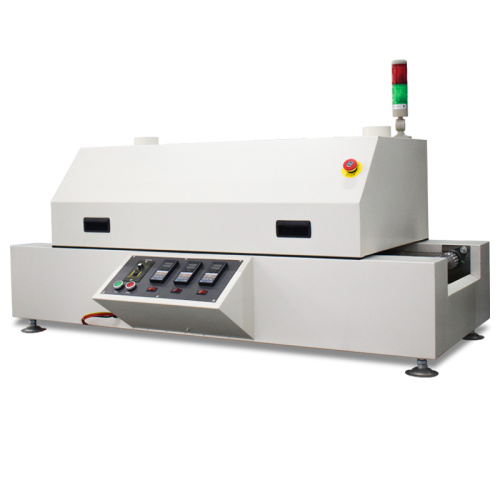
High quality small full hot air reflow soldering
- Transportation:
- Ocean
- Port:
- Yantian Port, Shenzhen
Your message must be between 20 to 2000 characters
Contact NowPlace of Origin: | China |
---|---|
Productivity: | 300 units/year |
Supply Ability: | Sufficient supply |
HS Code: | 8515190010 |
Transportation: | Ocean |
Port: | Yantian Port, Shenzhen |
High quality small full hot air reflow soldering
Due to the continuous miniaturization of PCB boards of electronic products, chip components have appeared, and traditional soldering methods can no longer meet the needs. At first, only the reflow soldering process was used in the assembly of hybrid integrated circuit boards, and most of the components to be assembled and soldered were chip capacitors, chip inductors, mounted transistors and diodes. With the development of the entire SMT technology becoming more and more perfect, and the emergence of a variety of chip components (SMC) and mount devices (SMD), the reflow soldering process technology and equipment as part of the placement technology has also been developed accordingly, and its applications are becoming more and more extensive. Almost all electronic products have been applied
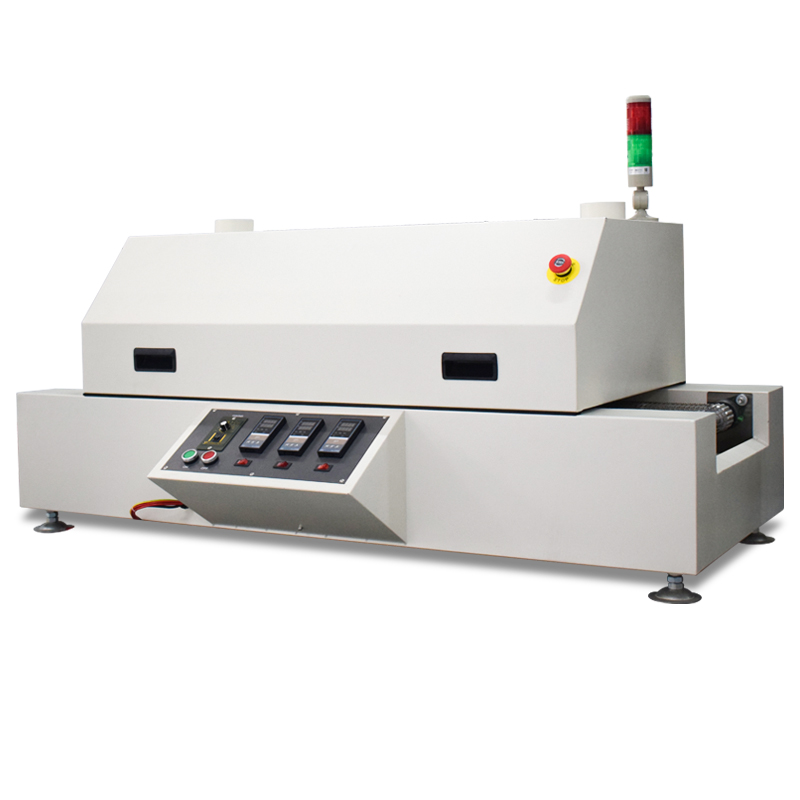
Model | MJ-H330A |
Parameters of heating part |
|
Number of heating zones | Up 3 down 0 |
Heating zone length | 100mm |
Heating mode | Full hot air |
Number of cooling zones | 1 |
Parameters of transportation |
|
Large width of PCB board | 300mm |
Transport direction | Left → right |
Height of conveyor belt | 350 ± 20mm |
Transmission mode | Net drive |
Speed of conveyor belt | 0-1200mm/min |
Parameters of control part |
|
Power supply | 5-wire 3-phase 380V single-phase 220V 50/60 Hz |
Startup power | 6KW |
Power consumption in normal operation | Approx.1. 5kW |
Heating time | About 15 minutes |
Temperature control range | Room temperature-310 ℃ |
Temperature control mode | PID Closed Loop Control, SSR Drive |
Temperature control accuracy | ± 1 ℃ |
Temperature distribution deviation of PCB board | ± 2 ℃ |
Anomaly alert | Abnormal temperature (ultra-high temperature or ultra-low temperature after constant temperature) |
Airframe parameters |
|
Exterior dimensions | L1500xW500xH650 |
Weight |
Approx.80Kg |
Company strength
Workshop shots
Item display
About delivery
All the equipment of the company includes freight and distribution fees, excluding the cost of going upstairs, depending on the distance, choose logistics consignment or door-to-door delivery
On-site installation and commissioning
The company is responsible for distribution, and there are professional engineers on-site installation, commissioning, training, or guidance and assistance through remote video or telephone
1 year warranty
After-sales promises that all parts of the wave soldering machine are guaranteed for one year, except for human problems
Lifetime service
The company provides life-long maintenance, paid service, only labor costs and material costs
Preparation before installation and commissioning
1. Door-to-door time: within 2 working days after all the following work is ready, special circumstances will be discussed separately
2. Logistics transportation: After receiving the goods, customers who choose logistics transportation must first place the equipment and prepare all the following materials
3. Home delivery: Customers who choose home delivery need to reserve space in advance to prevent equipment and prepare all the following materials
Material preparation:
1. Power connection: lead the power cord to the device according to the requirements of the device, leaving a length of more than 3 meters to connect to the device
2. Air connection: If there is an air source in the workshop, lead the air pipe to the side of the equipment, leaving a length of more than 3 meters to connect to the equipment. If there is no air source in the workshop, you need to prepare the air compressor in advance and prepare the necessary accessories
3. Tin bar: Prepare enough tin bars in advance according to the tin capacity requirements of the equipment, so that the master can directly melt the tin for on-site trial welding test and training when he comes to the door.
4. Flux: the flux that needs to be used when the product is ready for trial welding. At least 2 liters required for testing
5. Cleaning agent: the nozzle used to clean the flux, temporarily not used, it will not affect the debugging
Related Keywords