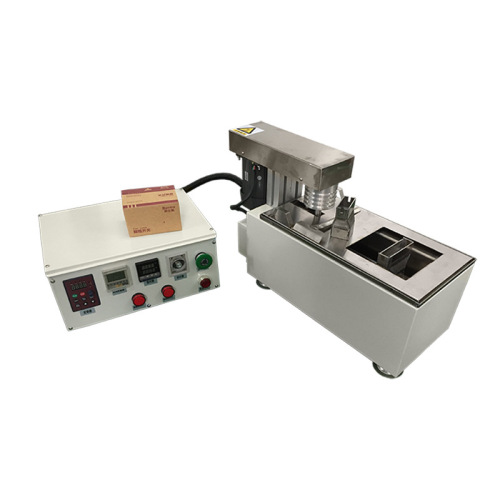
Desktop jet tin furnace
- Transportation:
- Ocean
- Port:
- Yantian Port, Shenzhen
Your message must be between 20 to 2000 characters
Contact NowPlace of Origin: | China |
---|---|
Productivity: | 300 units/year |
Supply Ability: | Sufficient supply |
HS Code: | 8515190010 |
Transportation: | Ocean |
Port: | Yantian Port, Shenzhen |
Desktop jet tin furnace
Model: TSPL3010 desktop |
Nozzle size: 60*60mm |
Melting tin volume: 21KG |
Tin furnace size: 300*100*100mm |
Starting power: 2.5KW |
Dimensions: 580*480*360mm |
Power supply: 220V 50HZ single phase |
Soldering time: 0-30 seconds adjustable |
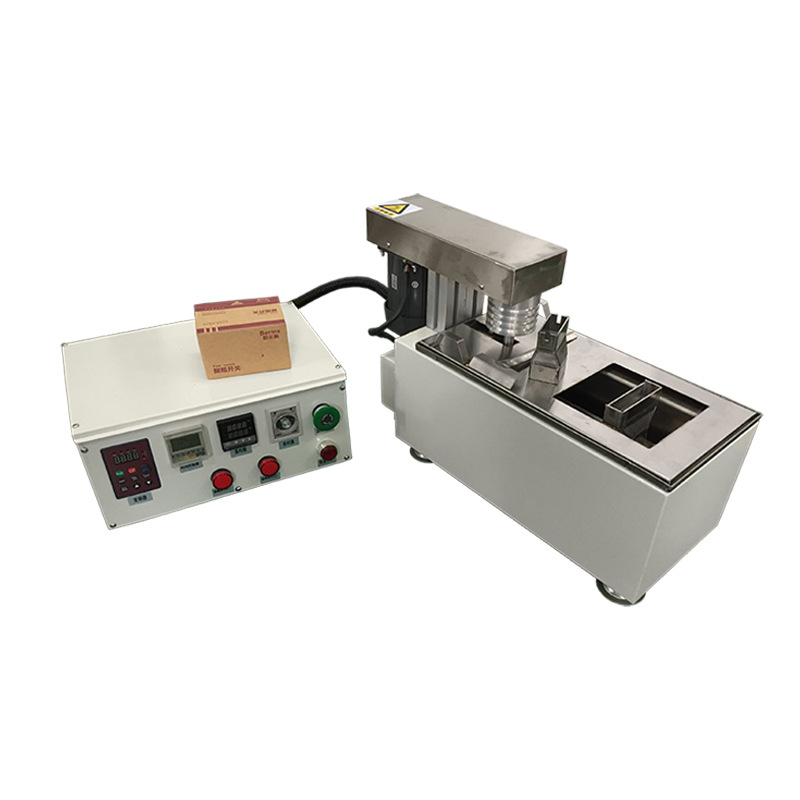
High-quality industrial pure titanium
The blade and runner tin bath materials are made of high-quality industrial pure titanium, which is resistant to high temperature and corrosion. The heating core is made of imported ceramic heating plate, which is durable
Digital display constant temperature
Adopting Yatai brand, PID control, SSR output, digital display constant temperature, using stepless frequency conversion technology, adjustable tin spraying time, adjustable tin spraying height
Removable spray nozzle
The plug-in replacement method replaces the spray nozzles, and chooses different sizes of nozzles according to the needs of the product
High temperature motor
The motor adopts Jinyong high temperature resistant motor, the power is 120W, the wave motor protection function, the motor cannot rotate when the tin temperature is not enough
Matters needing attention>
1. Input voltage: AC220V 50HZ
2. Be sure to ground before use, and it is forbidden to work without wires
3. It is recommended to set the first melting temperature to 80-150 degrees. After the tin starts to melt, slowly adjust the temperature to the required temperature. It takes about 20-30 minutes for the temperature to reach the set temperature. The height of the molten tin should be about 5mm away from the top of the tin furnace. Wait until the tin is completely melted before you can do soldering work
4. The power must be turned off before leaving to avoid accidents
Daily maintenance>
1. Every day, when the work is finished, be sure to clean the oxides in the tin bath to keep the tin bath and the tin furnace shell clean for a long time
2. When adjusting the temperature parameters and pressing the switch, be careful not to use too much force to avoid damage to the switch. The tin in the tin bath should be kept in sufficient quantity, because the temperature sensing point is about the middle height of the tin bath, and too little molten tin will cause temperature detection deviation
Workshop shots
Item display
About delivery
All the equipment of the company includes freight and distribution fees, excluding the cost of going upstairs, depending on the distance, choose logistics consignment or door-to-door delivery
On-site installation and commissioning
The company is responsible for distribution, and there are professional engineers on-site installation, commissioning, training, or guidance and assistance through remote video or telephone
1 year warranty
After-sales promises that all parts of the wave soldering machine are guaranteed for one year, except for human problems
Lifetime service
The company provides life-long maintenance, paid service, only labor costs and material costs
Preparation before installation and commissioning
1. Door-to-door time: within 2 working days after all the following work is ready, special circumstances will be discussed separately
2. Logistics transportation: After receiving the goods, customers who choose logistics transportation must first place the equipment and prepare all the following materials
3. Home delivery: Customers who choose home delivery need to reserve space in advance to prevent equipment and prepare all the following materials
Material preparation:
1. Power connection: lead the power cord to the device according to the requirements of the device, leaving a length of more than 3 meters to connect to the device
2. Air connection: If there is an air source in the workshop, lead the air pipe to the side of the equipment, leaving a length of more than 3 meters to connect to the equipment. If there is no air source in the workshop, you need to prepare the air compressor in advance and prepare the necessary accessories
3. Tin bar: Prepare enough tin bars in advance according to the tin capacity requirements of the equipment, so that the master can directly melt the tin for on-site trial welding test and training when he comes to the door.
4. Flux: the flux that needs to be used when the product is ready for trial welding. At least 2 liters required for testing
5. Cleaning agent: the nozzle used to clean the flux, temporarily not used, it will not affect the debugging
Related Keywords