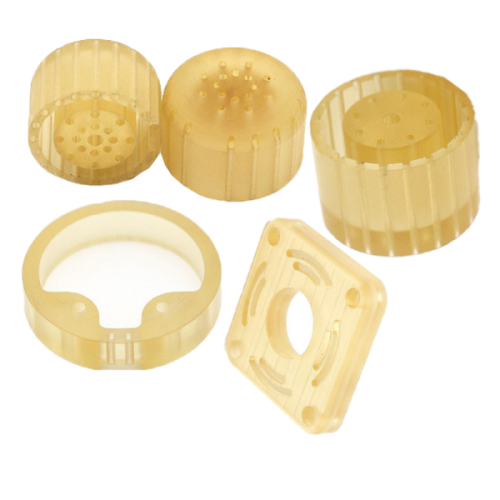
PPSU Injection Mould Part
- Min. Order:
- 1 Piece/Pieces
- Min. Order:
- 1 Piece/Pieces
- Transportation:
- Ocean, Land, Air, Express
- Port:
- Shenzhen, Guangzhou, Hongkong
Quantity:
Your message must be between 20 to 2000 characters
Contact NowBasic Info
Basic Info
Supply Ability: | 1000 |
---|---|
Payment Type: | T/T,Paypal |
Incoterm: | FOB,CFR,CIF,EXW,DDP,DDU |
Transportation: | Ocean,Land,Air,Express |
Port: | Shenzhen,Guangzhou,Hongkong |
Product Description
Product Description
PPSU processing and molding conditions
1, Molding temperature
The melting point of PPSU is about 260°C, so the key to the molding process is to control the heating temperature. Ideal molding temperature is usually between 180 ° C to 230 ° C. The molding temperature can be too high or too low. Too high or too low a temperature may lead to material decomposition or deformation.
2, Pressure and speed
Due to the poor fluidity of the melt of PPSU, the need for higher injection pressure (usually 150-400MPa) and slower injection speed (10-30mm per second) to ensure that the molten material can fully fill every corner of the mold.
3, Mold design
Due to the close molecular structure of PPSU and high crystallinity, the design should pay attention to avoid the melt in the cooling process of contraction and deformation. It is recommended to use a short runner, wall thickness of the mold design to ensure uniform filling and rapid cooling of the melt.
4, Post-processing
After molding PPSU plastic needs to be post-treatment, such as drying and curing, to remove residual moisture and volatiles, so that the material becomes more hard and stable.
5, Other Precautions
During the injection molding process, the injection speed and pressure, as well as the mold temperature and cooling conditions, should be strictly controlled to prevent the occurrence of bubbles, shrinkage and other problems. In addition, the poor fluidity of PPSU material requires the use of high viscosity screws and nozzles.
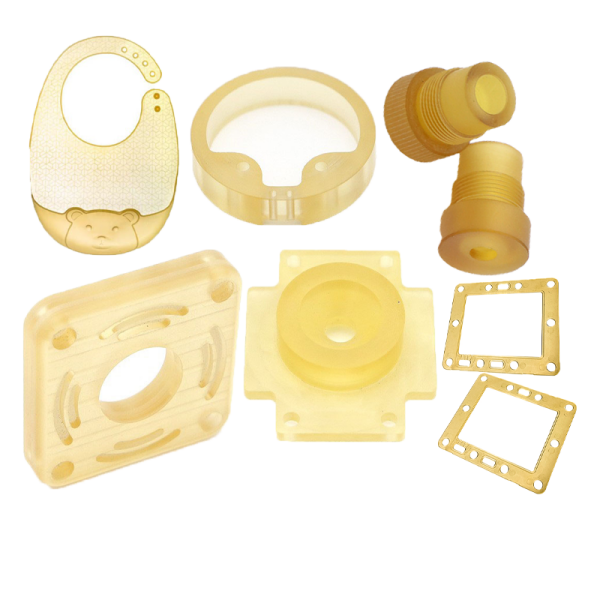
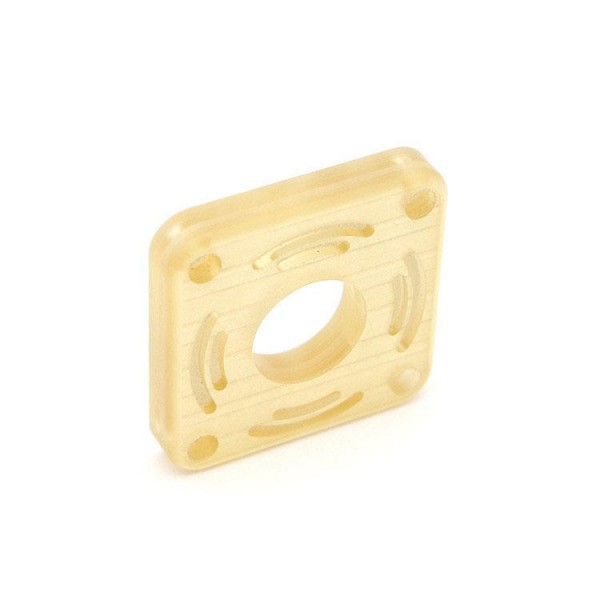
PPSU polyphenylsulfone specialty plastics provide high-precision solutions through the precision injection molding process to meet the high requirements of industries such as aerospace. The main differences between its precision injection molding and normal injection molding are design requirements, manufacturing process and application areas.
PPSU polyphenylsulfone is a special engineering plastic with high transparency and hydrolytic stability, which can provide compatible solutions for various industries through the injection molding process, which is more popular than PSU injection molded parts, PES injection molded parts and PEI injection molded parts.
Relative to the cutting-edge industry, ordinary injection molding process precision has been unable to meet customer requirements, so PPSU precision injection molding process from the design requirements, manufacturing process, mold life, cost-effective and other aspects of making new changes.
PPSU precision injection molding requirements:
1. design requirements: ppsu products processing on the injection mold requirements are higher, in order to ensure that the production of high-precision, high-quality products, the dimensional accuracy of the mold and the surface finish and mold life put forward higher requirements.
2. Material selection: PPSU injection molding parts are usually selected high hardness, high wear-resistant materials to make molds, in order to meet the demand for long time and high intensity injection molding production.
3. Mold life: PPSU precision injection molds due to the production process to withstand higher pressure and wear, so the cycle life is relatively short, generally in the tens of thousands to hundreds of thousands of injection cycles.
4. Cost-effectiveness: PPSU precision injection molding process has higher requirements for the mold, the initial cost is large, and after mass production, the maintenance cost and the use of the cost is relatively small.
5. Application areas: PPSU precision injection molded parts for high-precision industries: aerospace, automotive parts, precision instruments, analytical testing and other high-precision, miniaturized parts and components have higher requirements of industrial supplies, ordinary injection molding is not up to this requirement.
Summarize
PPSU precision injection molding parts and ordinary injection molding processing is the main difference between its design requirements, manufacturing process, and application areas, PPSU precision injection molding is suitable for the product precision and quality control requirements of the field of extremely high, ordinary injection molding is suitable for a wide range of applications.
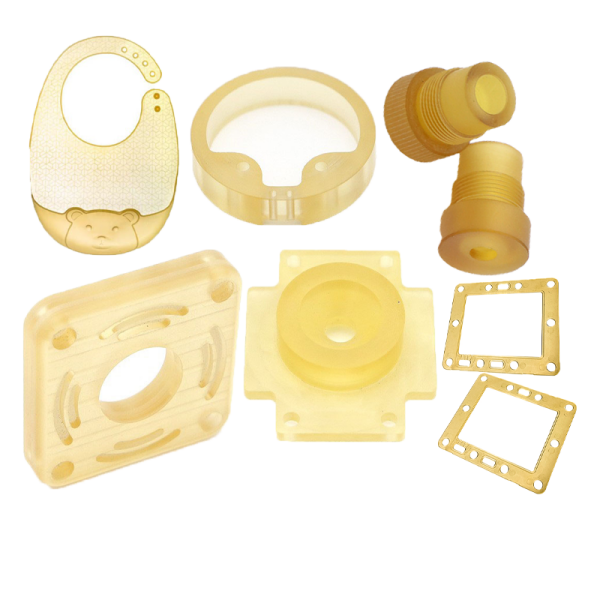
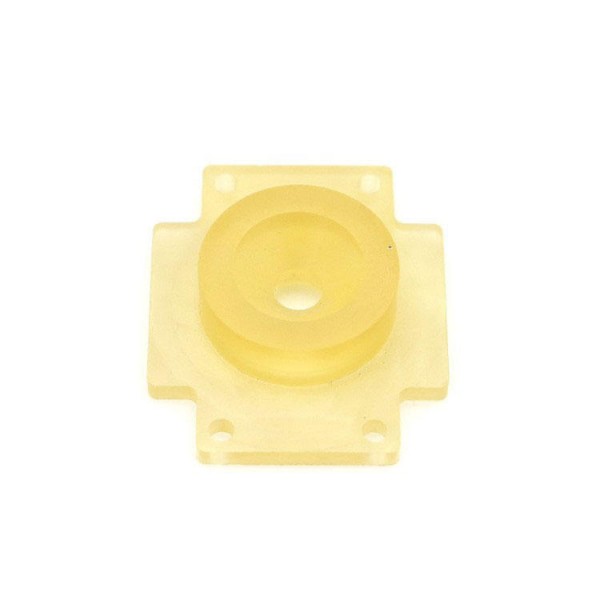

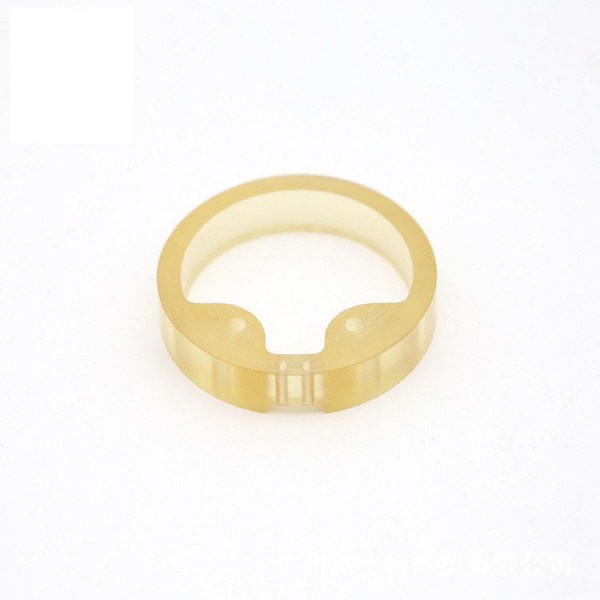
Characteristics of PPSU blister processing thermoforming
1, Excellent material properties
PPSU has high heat resistance, chemical resistance and excellent mechanical properties, to meet the needs of a variety of complex shapes and high demand for products.
2, Strong customizability
By adjusting the heating temperature, molding pressure and mold design and other parameters, in order to manufacture products of different sizes, shapes and thicknesses. At the same time, can be added in the molding process, such as reinforcing bars, threads and other structures to improve the mechanical properties and functionality of products.
3, Lower processing costs
Compared with injection molding and other molding processes, blister thermoforming equipment and mold costs are lower, and the production process consumes less energy, which helps reduce production costs.
4, Environmentally sustainable
PPSU is an environmentally friendly material that can be recycled. At the same time, the blister thermoforming process produces less waste, helping to reduce environmental pollution.
5, Wide range of applications
PPSU blister thermoforming products can be used in medical, food, cosmetics, electronic products and many other fields, the market demand is high.
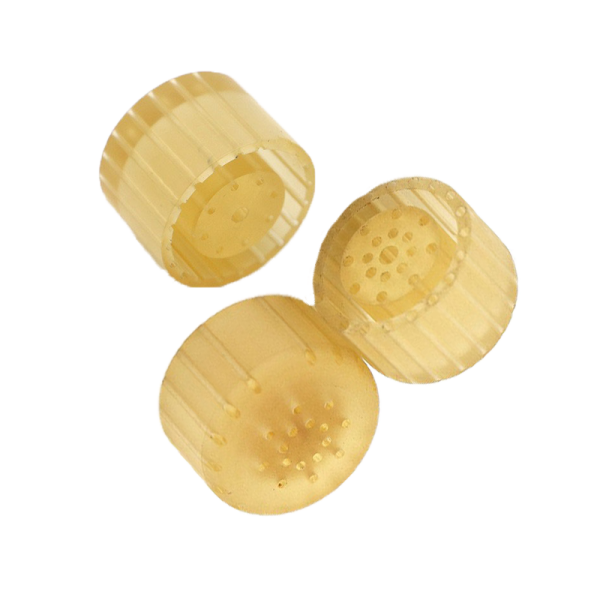
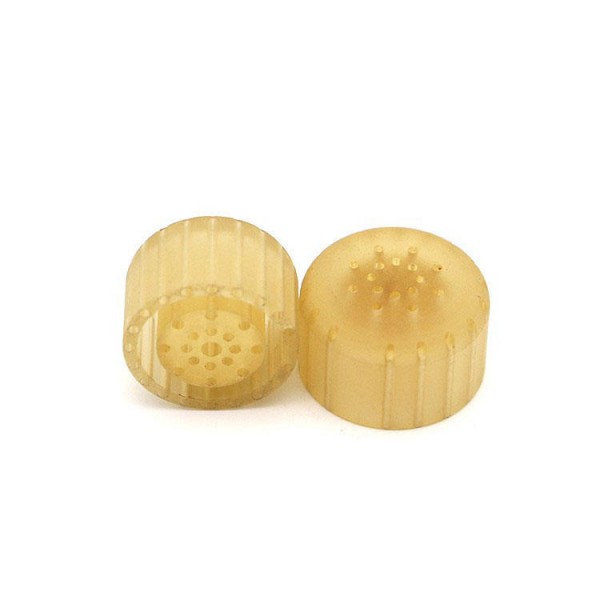
PPSU products processing common problems and their solutions
1, The emergence of air bubbles
Bubbles are common PPSU products is mainly due to the mold temperature is too high or the injection speed is too fast. The solution is to reduce the mold temperature, slow down the injection speed, and at the same time can increase the injection time and the second stage of the injection time, in order to allow the gas to have enough time to discharge the mold.
2, Shrinkage
PPSU products in the cooling process will appear shrinkage, if too much shrinkage will lead to product deformation. The solution is to increase the mold temperature during processing, slow down the cooling rate, while you can increase the injection time and injection pressure in order to allow the material to better fill the mold cavity.
3, Cracks cracks
Mainly due to unreasonable mold design or mold temperature is too low. The solution is to check whether the mold design is reasonable, if there is any problem timely modification. At the same time can be appropriate to improve the mold temperature and processing temperature, slow down the injection speed, in order to let the material flow better and fill the mold cavity.
4, The appearance of silver silver grain
Is due to excessive moisture or volatiles in the PPSU material, the solution is to check whether the material is dry, to ensure that there is no moisture or volatiles in the material. At the same time, you can appropriately increase the mold temperature and processing temperature, increase the injection time and injection pressure, in order to allow the material to flow better and fill the mold cavity.
5, The appearance of opacity or color inconsistency
Is due to the quality of PPSU material problems, the solution is to check whether the material is qualified, if any problem timely replacement. At the same time can be appropriate to increase the processing temperature and extend the processing time, in order to let the material better plasticization and uniform mixing.
Related Keywords
Related Keywords