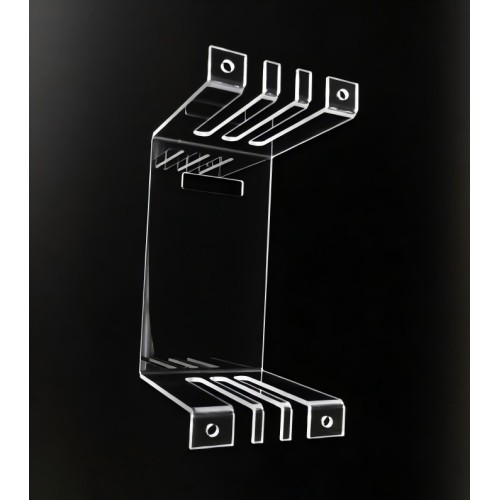
PC Polycarbonate Processing and Molding Fabrication Services
- Min. Order:
- 1 Piece/Pieces
- Min. Order:
- 1 Piece/Pieces
- Transportation:
- Ocean, Land, Air, Express
- Port:
- Shenzhen, Hongkong, Guangzhou
Quantity:
Your message must be between 20 to 2000 characters
Contact NowBasic Info
Basic Info
Supply Ability: | 1000 |
---|---|
Payment Type: | T/T,Paypal |
Incoterm: | FOB,CFR,CIF,EXW,DDP,DDU |
Transportation: | Ocean,Land,Air,Express |
Port: | Shenzhen,Hongkong,Guangzhou |
Product Description
Product Description
Polycarbonate plastic, a type of plastic primarily composed of polycarbonate. Polycarbonate is an amorphous polymer that transforms into a transparent glass-like substance after melting and cooling, exhibiting excellent optical and mechanical properties. It has a high melting point, can withstand low temperatures, has low water absorption, and demonstrates good impact resistance, insulation properties, and resistance to aging. It is also resistant to inorganic and organic dilute acids.
It can be used to manufacture signs, instrument housings, furniture, automotive headlights, electrical components, instrument panels, and more. The use of polycarbonate as a substrate for optical discs has seen significant growth.
Chinese name Polycarbonate plastic
English name Polycarbonate Plastic
Brief description A plastic primarily composed of polycarbonate
Properties
Excellent heat resistance, cold resistance, and electrical properties
Glass transition temperature: 149–150°C
Applications
Mechanical, electronic, and electrical industries, transportation, etc.
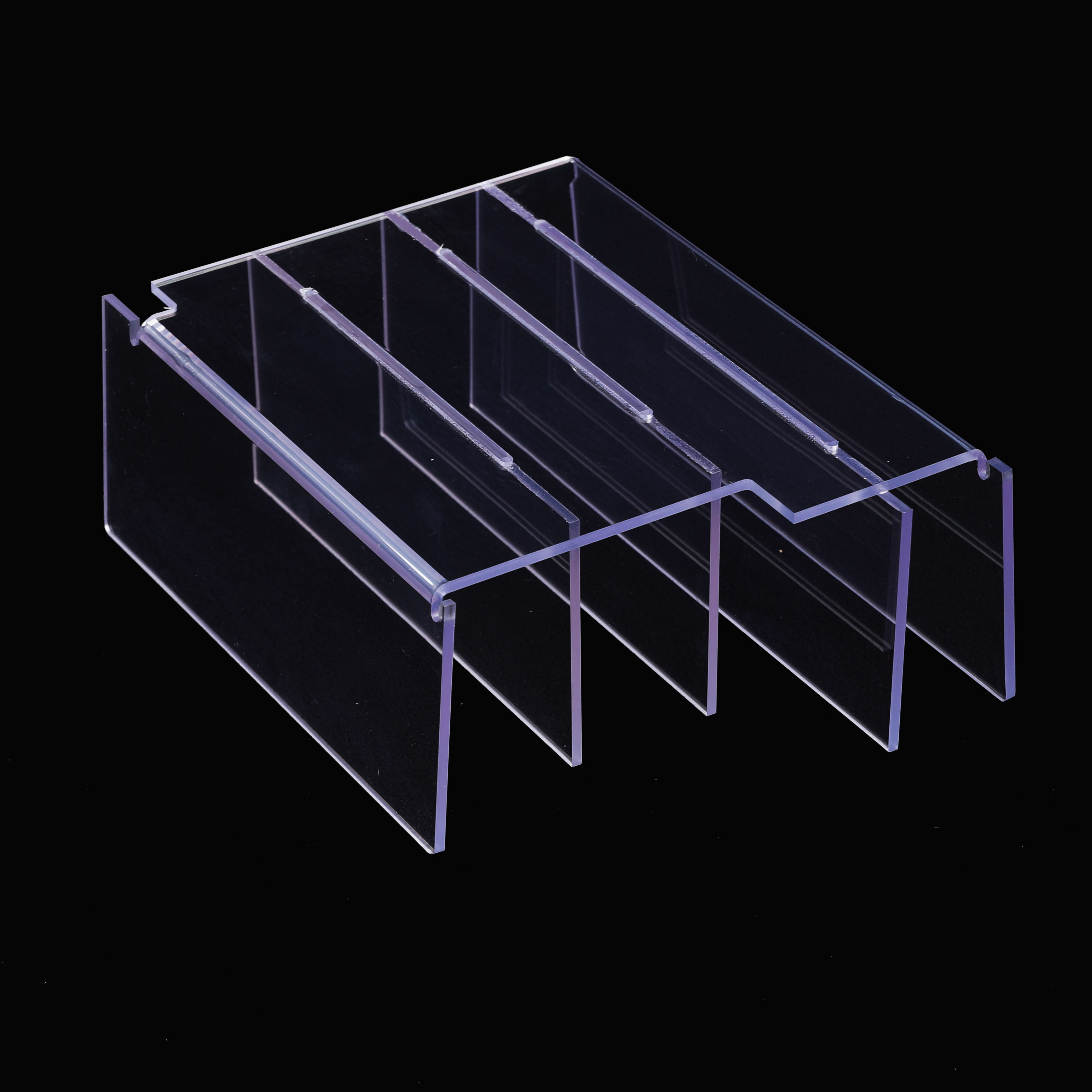
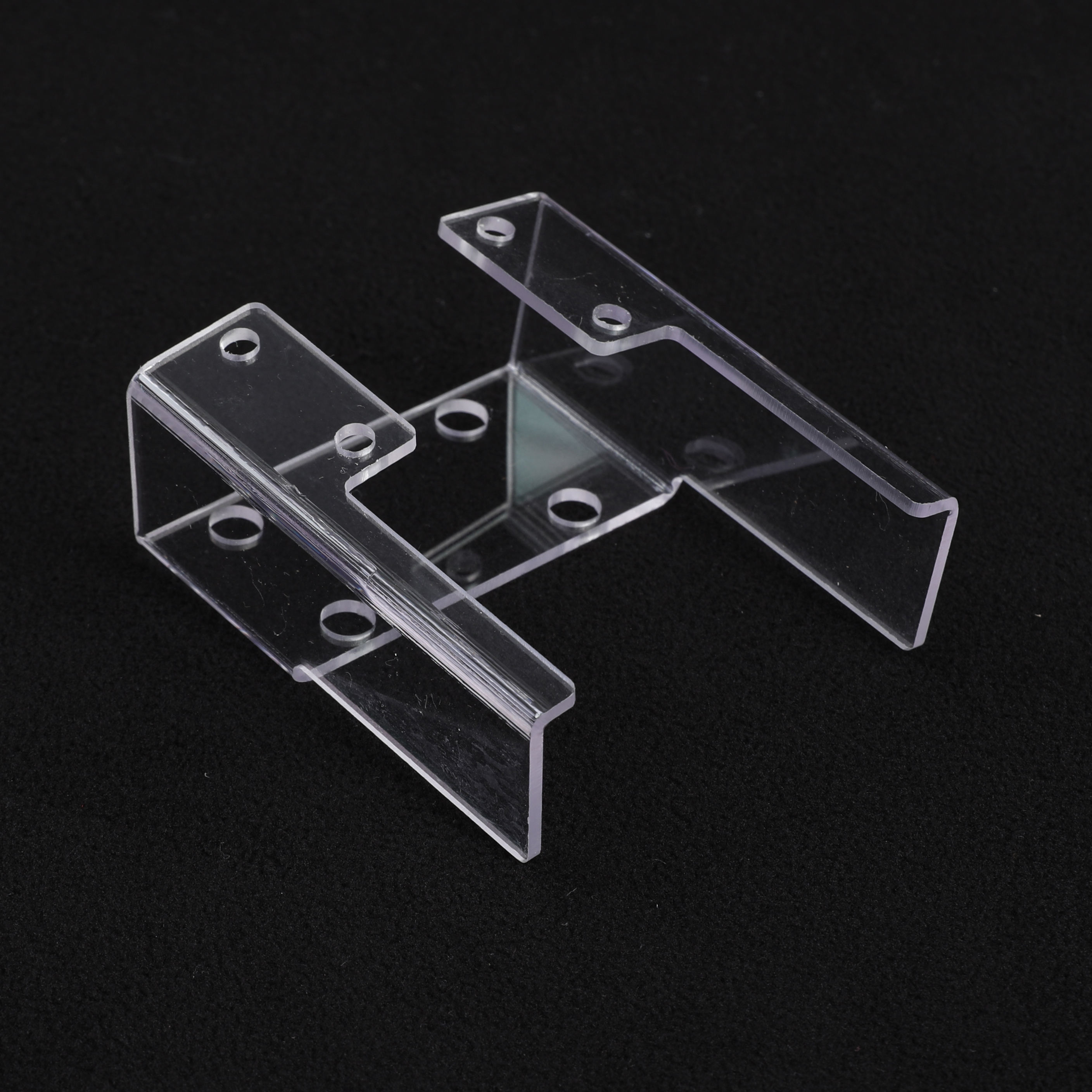
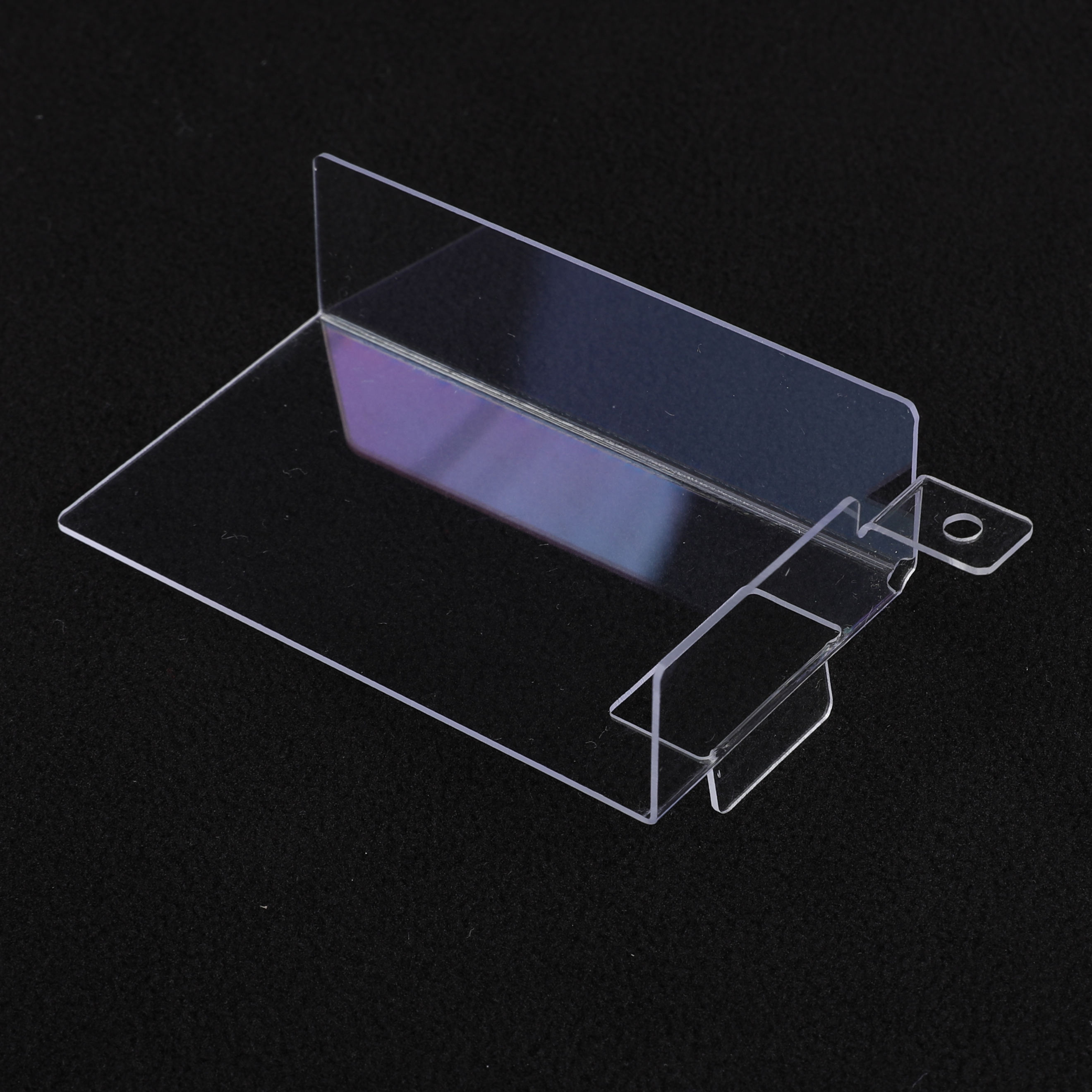
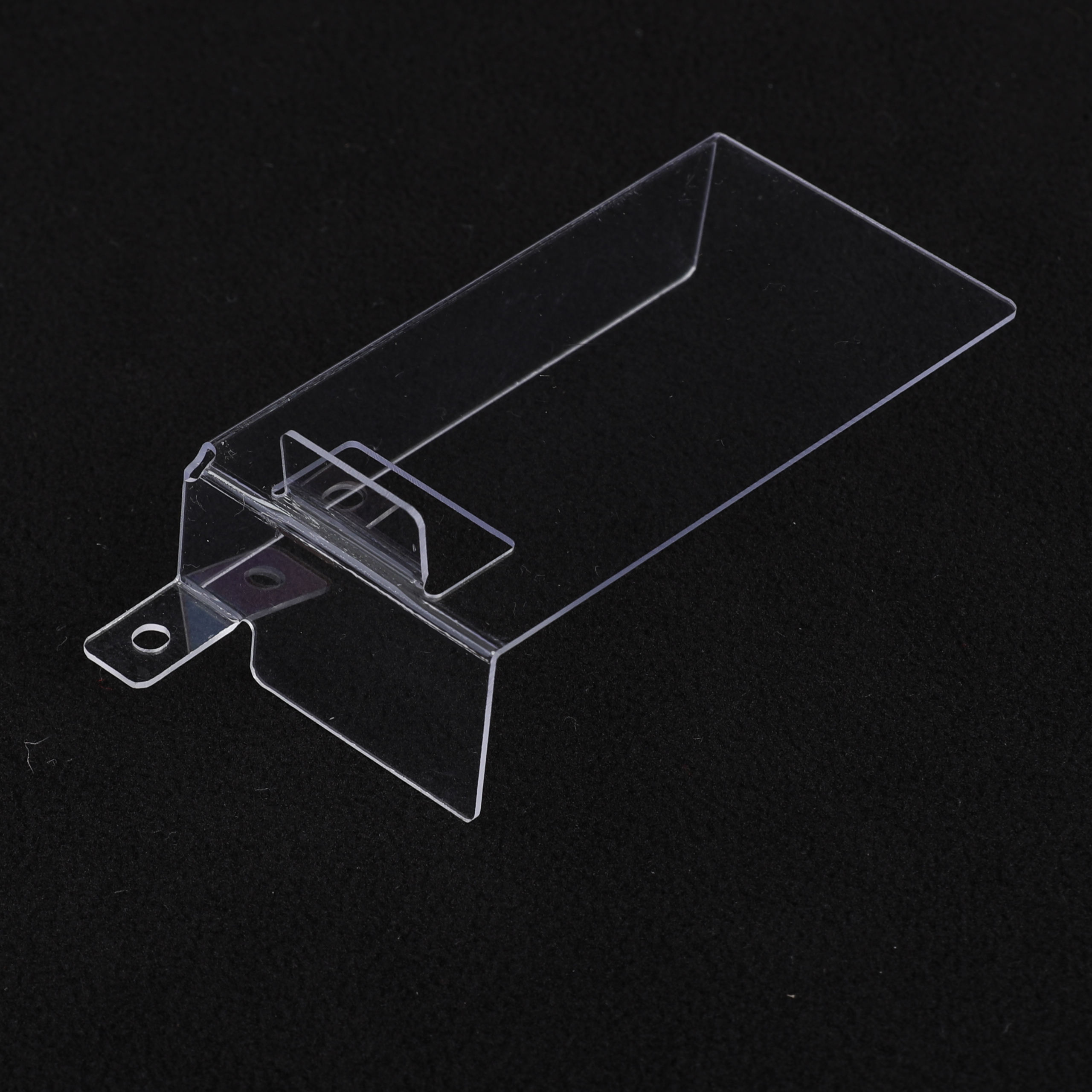
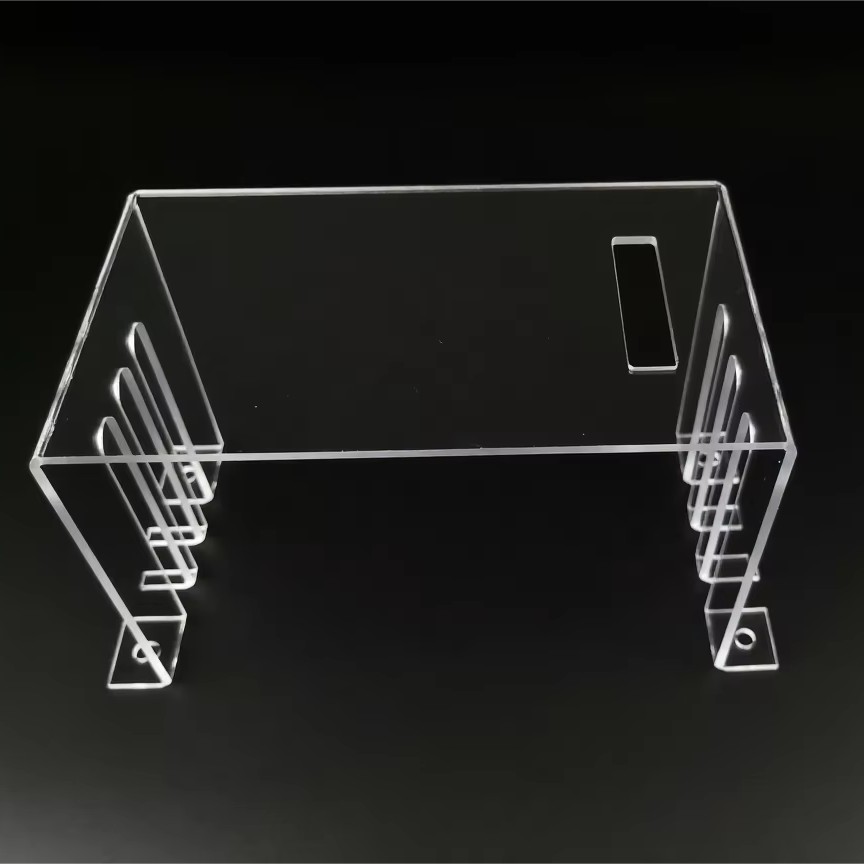
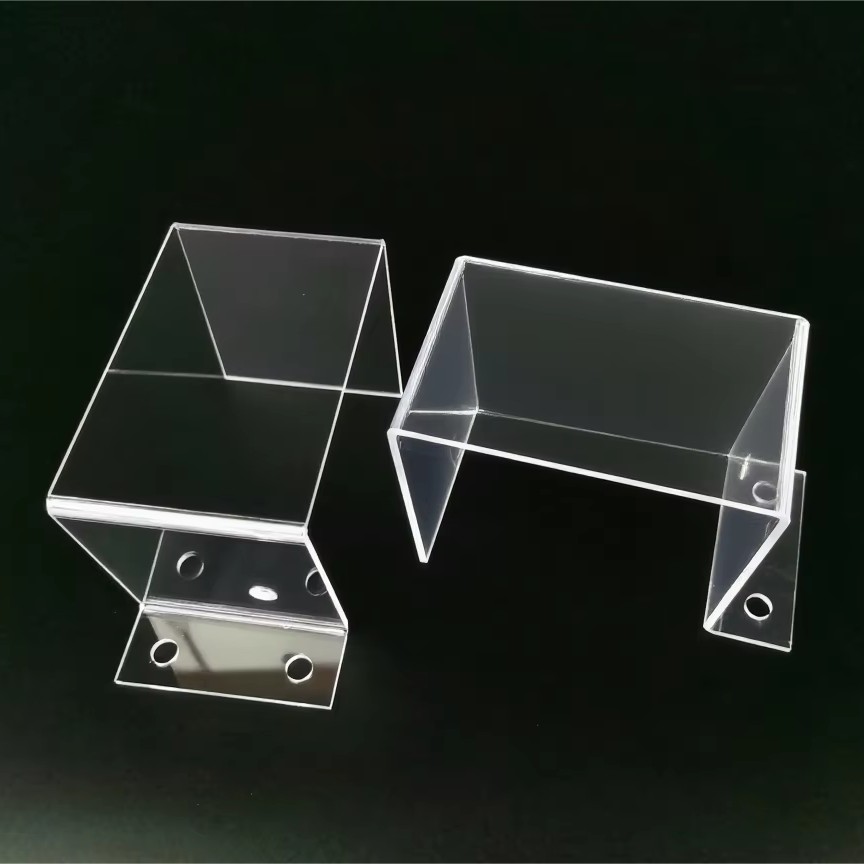
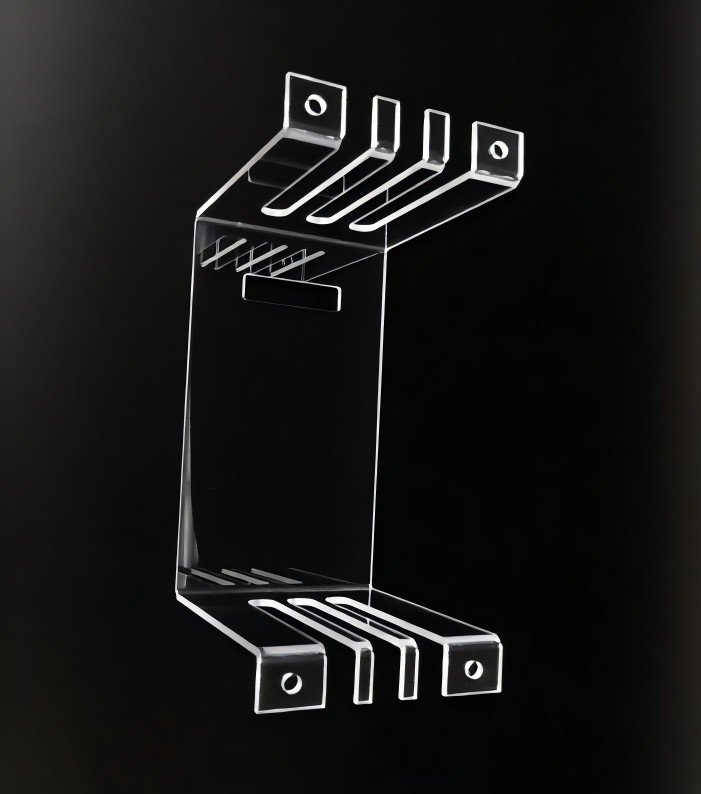
Table of Contents
1 Introduction
2 Molding Process
3 Properties and Characteristics of Polycarbonate
4 Product Molding Methods
5 Applications
Although polycarbonate has good toughness and mechanical properties, it has poor resistance to environmental stress cracking and high notch sensitivity, making it difficult to form parts with metal inserts.
Polycarbonate plastic has a low tendency to crystallize and no precise melting point, and is generally considered a non-crystalline plastic. Its glass transition temperature is relatively high at 149–150°C, with a melting temperature of 215–225°C, and the molding temperature can be controlled between 250–310°C.
The thermal stability and mechanical strength of polycarbonate increase with rising relative molecular weight, and its melt viscosity also significantly increases with rising relative molecular weight. The relative molecular weight of polycarbonate used for injection molding is generally 20,000–40,000.
The melt viscosity of polycarbonate is much higher than that of nylon, polystyrene, and polyethylene, which affects injection molding because the flow length decreases as viscosity increases. Its flow characteristics are similar to those of a Newtonian fluid, with melt viscosity being less affected by shear rate but highly sensitive to temperature changes. Therefore, during injection molding, increasing the temperature to reduce viscosity is more effective than increasing pressure.
Molding Process
1. Preheating and Drying of Raw Materials
To ensure the quality of the molded parts, the raw materials must be thoroughly dried before molding. Drying methods include fluidized bed drying (temperature 120–130°C, time 1–2 hours); vacuum drying [temperature 110°C, vacuum pressure 0.96 MPa (720 mmHg) or higher, time 10–25 hours]; or conventional oven drying (temperature 110–120°C, time 25–48 hours). Drying time should not be excessive, as prolonged drying can darken the resin color and impair performance. Moisture content after drying should not exceed 0.03%. During injection, the hopper should be sealed and may be equipped with a heating device (infrared lamp or electric heater), with the material temperature allowed to reach 120°C to prevent the dried resin from reabsorbing moisture. The hopper’s feed rate should not exceed the amount required for 0.5–1 hours of use. Dried material that is not immediately used should be stored in a sealed container. When using, it should be dried again at 120°C for more than 4 hours. A quick method to check moisture content compliance is to use the “empty injection” method on the injection machine. If the material slowly flowing from the nozzle is uniform, colorless, glossy, free of silver threads, and bubble-free, it is considered
2. Molding Temperature
The selection of molding temperature is related to the resin's molecular weight and its distribution, the shape and wall thickness of the part, and the type of injection molding machine, generally controlled within the range of 250–310°C. Injection molding is best suited for resins with slightly lower molecular weights, though this may result in reduced toughness. The K-value of the selected resin should ideally be between 52 and 54. For thin-walled parts, the molding temperature should be higher, preferably between 285 and 305°C; for thick-walled parts (wall thickness greater than 10 mm), the molding temperature can be slightly lower, ideally between 250 and 280°C. Due to the longer molding cycle for thick-walled parts, the plastic is better plastified in the barrel; additionally, the gate and cavity dimensions for thick-walled parts are larger, resulting in lower flow resistance for the plastic melt, allowing molding at slightly lower temperatures. If the temperature exceeds 290°C, the injection cycle lengthens, increasing the tendency for overheating and decomposition, which can impair the overall performance of the part. Different types of injection molding machines have different molding temperatures: screw-type machines range from 260°C to 285°C, while plunger-type machines range from 270°C to 310°C. The nozzles on both types of injection molding machines should be heated to a temperature of 260–310°C. The barrel temperature at the feed end should be above the softening temperature of polycarbonate, typically above 230°C, to reduce material blockage resistance and injection pressure loss.
3. Injection Pressure
Polycarbonate has a high melt viscosity, so molding thin-walled or complex-shaped parts requires higher injection pressure. For plunger-type injection molding machines, the injection pressure is generally 100–160 MPa, while for screw-type injection molding machines, it is 80–130 MPa. Holding pressure time significantly affects internal stress in the part. To achieve parts with good performance, using high material temperature and low pressure is appropriate, which reduces residual pressure in the part. Excessively long holding pressure time not only results in high internal stress, causing the part to crack and reduce strength, but also extends the molding cycle. Typically, the injection speed is approximately 8–10 m/s.
4. Mold Temperature
Internal stress in the part is generally proportional to the difference between the material temperature and mold temperature during cooling. Therefore, the mold temperature should be as high as possible. Polycarbonate plastic parts can be demolded smoothly at a mold temperature of 140°C, so the mold temperature is generally maintained between 85–140°C. If the mold temperature is too high, the part cools slowly, the molding cycle is prolonged, and sticking may occur, causing deformation during demolding.
5. Thermal treatment of parts
Internal stress in polycarbonate parts can be eliminated through thermal treatment. The thermal treatment temperature should be selected 16–20°C below the glass transition temperature, typically controlled at 125–135°C. The treatment time depends on the thickness and shape of the part; thicker parts require longer treatment times.
Properties and characteristics of polycarbonate
Polycarbonate (PC) is a general term for high-molecular-weight compounds containing carbonate ester chains in the main chain of the polymer. PC is the abbreviated code for polycarbonate. The production methods for polycarbonate include ester exchange and phosgene-based synthesis. Currently, the most widely used and versatile types are bisphenol A-type aromatic polycarbonates and engineering plastics reinforced with glass fiber.
Polycarbonate is a transparent, white, or slightly yellow polymer that is amorphous, odorless, and non-toxic; the finished products are rigid, impact-resistant, and have good toughness with low water absorption; they also exhibit excellent mechanical properties. However, it has low fatigue strength and is prone to cracking; it has good heat resistance and cold resistance, with an application temperature range of -60°C to 120°C, a heat deflection temperature of approximately 135°C, melts at temperatures between 220°C and 230°C, and decomposes at temperatures above 310°C; the molten material has high viscosity, poor flowability, and is difficult to process, but it has good colorability; It has good electrical insulation properties, is non-flammable, and has self-extinguishing properties; it is resistant to acids, salts, oils, aliphatic hydrocarbons, and alcohols, but not resistant to chlorinated hydrocarbons, alkalis, amines, ketones, and other media; it is soluble in chlorinated hydrocarbon solvents such as dichloromethane and dichloroethane.
Molding methods for products
Before molding polycarbonate products, the raw material should be dried in a hot air circulation oven at 120–130°C for approximately 10 hours to reduce the moisture content to less than 0.03%.
After drying, the raw material can be processed using methods such as extrusion, injection molding, blow molding, and vacuum forming to produce various products such as sheets, tubes, containers, and films.
During polycarbonate molding, the barrel's feeding section temperature is around 230°C, the plasticizing section temperature is around 250°C, the homogenization section temperature is around 270°C, the injection pressure is within the range of 40–120 MPa, and the mold temperature is around 100°C. To eliminate internal stress in the finished product, it should undergo heat treatment at a temperature of around 120°C after molding. Heat treatment can be performed using an oil bath method or in an oven.
Applications
Polycarbonate is an engineering plastic with excellent comprehensive properties, and its products are widely used in the mechanical, electrical, transportation, textile, medical, and daily consumer goods industries.
① In the mechanical field, it is used for various parts with relatively low working loads, such as gears, racks, cams, worms, screws, nuts, fittings, impellers, valve components, photographic equipment components, and watch components.
② In the electronics and electrical appliance industry, it is used for insulated connectors, coil frames, gaskets, etc., in electronic computers, televisions, radios, audio equipment, and household appliances, as well as instrument housings, drill housings, hair dryers, lighting fixtures, and controllers.
③ In daily necessities, it is used for sunglasses, lighters, smoking accessories, bathtubs, helmets, lampshades, tableware, signal lamp bodies, and beer bottles.
④ Military applications, including aircraft, automotive, and marine windshields, anti-tank mines, firearm grips, periscopes, etc.
⑤ Other applications, such as various weft tubes, yarn tubes, and wool spinning tubes for the textile industry, as well as high-impact-strength glass windows and glass greenhouse equipment in construction and agriculture, offering high safety and decorative value.
Related Keywords
Related Keywords