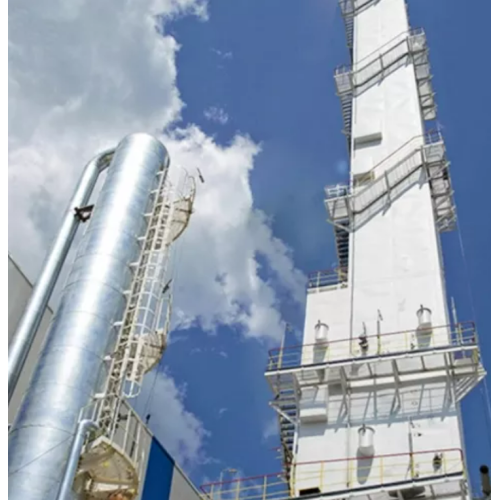
High Purity Oxygen Nitrogen Production ASU Plant
- Transportation:
- Ocean, Land, Air
Your message must be between 20 to 2000 characters
Contact NowPayment Type: | T/T |
---|---|
Incoterm: | FOB |
Transportation: | Ocean,Land,Air |
Product Description
Process Description
The air passes through the air filter, enters the air compressor, compresses to 0.7mpa in the compressor, and then enters the purifier after cooling, where the impurities such as water, carbon dioxide and acetylene in the air are removed. The purified air enters the heat exchanger for heat exchange with the backflow polluted nitrogen. A part of the gas is pumped into the turbine expander through the outlet of the heat exchanger, and the expansion provides a cooling source for the whole set of devices. The other gases continue to cool through the second heat exchanger and then enter the rectifying tower, where they are separated by oxygen and nitrogen. Finally, qualified liquid nitrogen is obtained from the top of the rectifying tower. After decompression by the throttle valve, the liquid air at the bottom enters the condensing evaporator at the top of the tower and the nitrogen heat exchange at the top of the rectifying tower, and then passes through the cooler, the second heat exchanger and the main heat exchanger cooling box as the regenerative purifier.
Cryogenic oxygen air separation unit(KDO)
Name
Oxygen
Pressure
20MPaG(adjustable)
Purity
≥99.6%
Operation Cycle
12months
Start time
~24hours
Single column, internal compression process
Cryogenic oxygen&nitrogen air separation unit(KDON)
Name
Oxygen&Nitrogen gas
Pressure
20MpaG(adjustable)
Oxygen purity
≥99.6%
Nitrogen purity
≥99.99%
Start pressure
1.0MPaG
Double column, external compression process
Model
Unit
KPDON
-50-50
KPDON
-80-160
KPDON
-180-300
KPDON
-260-500
KPDON
-350-700
KPDON
-550-1000
KPDON
-750-1500
KPDONAR
-1200-3000-30Y
Oxygen production
Nm³/h
50
80
180
260
350
550
750
1200
Oxygen purity
%O₂
≥99.6
≥99.6
≥99.6
≥99.6
≥99.6
≥99.6
≥99.6
≥99.6
Nitrogen production
Nm³/h
50
160
300
500
700
1000
1500
2000
Nitrogen purity
PpmO₂
≤10
≤10
≤10
≤10
≤10
≤10
≤10
≤5
Liquid argon production
Nm³/h
-
-
-
-
-
-
-
30
Liquid argon purity
PpmO₂
+Ppmn₂
-
-
-
-
-
-
-
≤1.5PpmO₂+3PpmN₂
Liquid argon pressure
Mpa.A
-
-
-
-
-
-
-
0.2
Unit consumption
Kwh/Nm³O₂
≤1.3
≤0.85
≤0.68
≤0.68
≤0.65
≤0.65
≤0.63
≤0.55
Device occupied area
m²
145
150
160
180
250
420
450
800
Main Equipment of Cryogenic Air Separation Plant:
Special Features of ASU Plant:
- A few of the latest technological features incorporated into the Oxygen & Nitrogen plants are listed below.
- Purity of Oxygen produced from all plants is minimum 99.7% and Nitrogen Purity can be available up to 1-10 PPM (Depending upon requirement of the customer).
- All plants use "Oil free" rotary screw /centrifugal oil compressor working between 6-13 BAR.
- All plants incorporate Aluminum Brazed exchangers and packed columns for high efficiency.
- Turbo expanders (GAS Bearing) for trouble free operation.
- All plants can supplied with automatic PLC control.
- Engineering support along with complete quality control is provided by our company.
- We provide qualified engineers for Supervision, Installation and start up of all our plants as well as training of manpower at customers' site.
- Very low power consumption with proven performance and virtually easy maintenance required for the machines.
- 100% reliability for oxygen gas quality for industrial & hospital use.
Product Advantages
1. The compact and modular design of all systems ensures easy transportation and cheaper installation, fast project delivery time seamlessly connects with the customer team, minimizes project costs and optimizes project schedules.
2. Fully automated system for simple and reliable operation.
3. Guaranteed availablity of high-purity industrial gases.
4. Guaranteed by the availability of product in liquid phase to be stored for use during any maintenance operations.
5. Low energy consumption, simple installation and maintenance
6. Short time delivery, seamless operation with one team together with the clients to minimize project cost and optimize the proposal.
Whether you are producing steel or nonferrous metals, traditional petrochemicals, or running the most advanced gasification or oxy-fuel process for your clean energy application, your air separation plant plays a significant role in your operations. Our company has the technology, experience, and resources necessary to design, engineer, construct, and operate a cost-effective gas supply system for your specific application.
Related Keywords