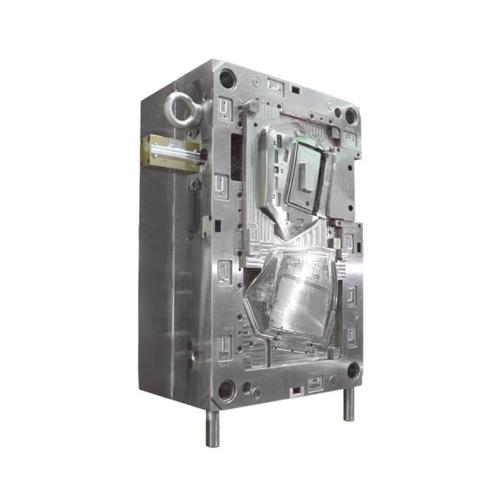
Plastic Injection Moulds
- Payment Type:
- T/T
- Incoterm:
- FOB
- Min. Order:
- 1 Set/Sets
- Min. Order:
- 1 Set/Sets
- Delivery Time:
- 49 Days
- Transportation:
- Ocean
- Port:
- Shenzhen
Your message must be between 20 to 2000 characters
Contact NowPlace of Origin: | China |
---|---|
Productivity: | 1000K shots |
Supply Ability: | 30 sets per month |
Payment Type: | T/T |
Incoterm: | FOB |
Certificate: | ISO 9001:2008 |
HS Code: | 8480719090 |
Transportation: | Ocean |
Port: | Shenzhen |
Thermoplastic Injection Molding Materials
ABS (Acrylonitrile Butadiene Styrene): A strong, rigid and tough material with good electrical properties and excellent chemical resistance. Both impact resistant and lightweight. Utilized in automotive, industrial, safety and consumer products.
Polystyrene: An economical and fairly rigid plastic. Used in both high volume production and prototyping. Seen in a wide variety of products, from molded packaging materials, aerospace and CD cases.
Polypropylene: An economical and rugged material that can be both flexible and tough. Great fatigue resistance and can be produced in a variety of colors. Utilized in automotive, medical, packaging, wire insulation and where plastic hinging is required.
Polyurethane: A resilient material with durability, toughness, abrasion resistance and resistant to flex fatigue. Good electrical characteristics, resistant to solvents and having a high load bearing capacity. Utilized in electronics, transportation, industrial, construction and consumer parts.
Acetal: A tough material with good heat resistance, rigidity and resistant to chemicals. Utilized in industrial, automotive, plumbing fixtures, telecommunications and consumer products.
LDPE (Low Density Polyethylene): Good tensile strength and ductility with excellent resistance to alcohols, bases and acids.
HDPE (High Density Polyethylene): A lightweight material with excellent durability, high tensile strength, corrosion and chemical resistant. HDPE has high impact resistance and low moisture absorption. Widely used in industrial, medical and consumer industries.
UHMW (Ultra High Molecular Weight Polyethylene): An extremely tough material with high abrasion and wear resistance. Popular for countless industrial applications that require durability, low friction and chemical resistance.
Polycarbonate: Combines outstanding strength, scratch resistance, durability and good mechanical properties with good optical properties. Used in eyeglass lenses, headlight covers, goggles, CD, food and beverage containers.
Nylon: PA 66, 6, 6/12 and 666. A very durable material that is resistant to abrasion, tough, high impact resistance, chemical resistant and UV resistant. Utilized in consumer goods, recreation, industrial, medical, automotive, military and electronics.
PEI: Polyetherimide is an amorphous engineering polymer capable of extreme temperature use. Polyetherimide provides outstanding electrical properties with stability over a wide variance of frequencies and temperatures. PEI is inherently flame retardant, and is also a low smoke generating polymer.
PEEK: Superb mechanical properties and is highly resistant to chemicals and thermal degradation. It holds up well against high temperatures and long-term liquid submersion, and is very durable in harsh environments. PEEK makes an excellent reinforcement material, providing great tensile strength and low weight.
Polysulfone: A semitransparent, heat-resistant, thermoplastic offering excellent mechanical, electrical and chemical resistance. Polysulfone properties remain relatively consistent over a broad range of temperatures, from -150°F to 300°F, and this material is suitable for applications where autoclavability is required.
Polyester: Combines high heat resistance, good impact strength, chemical resistance, good electrical properties, toughness, dimensional stability with flame retardant properties. Utilized in electronics, automotive, industrial and aerospace industries.
Project Information | ||
Product Description | Part Name | Automotive Door Bezel Tooling |
Part Material | PC+ABS | |
Part Size(mm) | 528.8x334.5x104 | |
Mould Description | Cavity Insert Material | 2344 HRC 52-54 |
Core Insert Material | 2344 HRC 52-54 | |
Slider Insert Material | 2344 HRC 52-54 | |
Mould Cavities | 1X2 | |
Mold parts Standard | Hasco | |
Mold Size | 1580x892x878mm | |
Mold weight | 5970kg | |
Lead time | 7 weeks | |
Mould Life Time (Shots) | 1000K | |
Mould Type | Export to Germany | |
Runner Description | Synventive Hot runner | |
Injection Gate Type | 4 Valve gates to cold runner | |
Ejection System | Ejector pin | |
Cycle time | 65s | |
Slide Qty. | 20 | |
Lifter Qty. | 0 | |
Injection moulding machine | 700T |
3K Mold is ISO-9001: 2008 certified. We use formal quality systems to manage the overall quality process and use precision measurement facilities by our well-trained team. All tooling and parts produced at our facility are constantly monitored by our Quality Assurance Department to meet your specifications.
Quality control Center
3K team committed to meet customer quality and delivery request. The main quality control process as following:
Incoming quality control (IQC)
In process quality control (IPQC)
Quality assurance (QA)
Quality management flow:
1. Mold base inspection
2. Steel inspection
3. Mold component inspection
4. Electrodes inspection
5. Mold checking before assembly
6. (FAI, CPK) First Article dimension report
7. Mold checking before delivery
Related Keywords