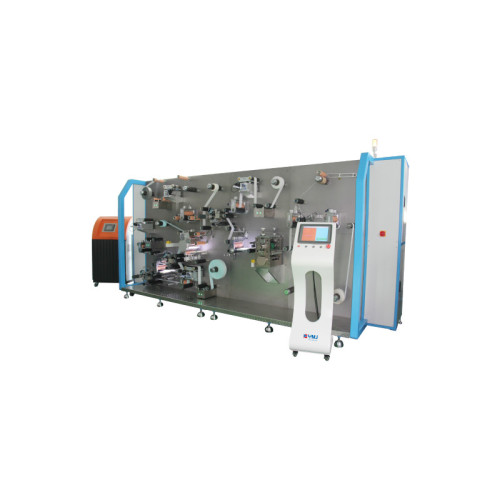
Full Auto RFID Converting Machine for Paper card
- Min. Order:
- 1 Set/Sets
- Min. Order:
- 1 Set/Sets
Your message must be between 20 to 2000 characters
Contact NowFull auto RFID converting machine is used for label converting and die cutting, 3 layers or 4 layers of roll to roll dry and wet inlay converting with label is optional. Inlay converting and die cutting with balance or imbalance printing layer just need to setting in software. It integrated of online gluing, converting, die cutting and testing. It applicable to roll label, paper card, swing tag, folding card and other product production. The solution of full auto modular system and multi-axis system which equip with Multi-axis synchronization function. Module configuration is reasonable, flexible and humanized combination. Machine has multi unit of tension and deviation correction systems which ensure the edges neatly, high output, high quality and high accuracy production for different products.
Main function:
1. Constant tension retracting roll ,with independent servo control ,break alarm protection ,and gas rising shaft automatic inflation.
2. There is a feeding platform in each layer, which is convenient for changing. User-friendly design, easy to operate.
3. The high-precision correction system is adopted, the ultrasonic sensor is monitored in real time, and the material in motion is corrected in real time. The correction accuracy is ±0.1mm, which ensures the composite precision of the label.
4. Each group of power units consists of anti-static and anti-adhesive rubber roller and precision hard oxide roller to prevent chip and material from being crushed during material movement.
5. After the material enters each power group, or composite, after the die cutting station, there is a set of ion static elimination mechanism to eliminate the static electricity generated in the material production and ensure that the chip or material is not damaged by static electricity.
6. Depending on the product, equipment 0-3 can be glued, and batch or continuous glue can be selected. The high-precision pressure regulating valve ensures the stability of the glue amount when the production speed is switched.
7. The unique cutting mechanism can cut off the antenna when it is used to produce antennas with different spacings , and then re-attach it to the coil. The sensor can monitor the position and the spacing can be set, which is flexible and convenient. In the production of wet Inlay, this mechanism can cooperate with the labeling mechanism, peel off the wet inlay and transfer it to the strip to achieve the wet inlay transfer.
8. After each layer of material is compounded or die-cut, a vision system can be added to detect the size of the composite and die-cutting on-line, and the alarm is automatically stopped.
9. There is a set of ion static elimination mechanism to eliminate the static electricity generated in the material production and ensure that the chip or material is not damaged by static electricity.
10. High-precision round die cutter, 2-3 sets of optional, high-precision sensors for precise positioning to ensure die cutting accuracy . Different shapes of die cutters are available for different products. Full or half cut can be selected for the roll label or tag.
11. HF or UHF card reader is optional, and the chip detection before receiving the chip. Bad mark inkjet dot making sign. Multiple sets of inspection and marking can be added after double-row or above product slitting.
12. According to different products, you can add cards or tags, bill receipts.
13. For small batch orders, an optional strip pull-down mechanism is available to adjust the die-cut spacing.
14. The die-cutting mechanism is equipped with a hydraulic detection system to detect the die-cutting pressure in real time, control the die-cutting depth, and ensure the die-cutting accuracy.
15. The gap between each group of composite rollers can be adjusted according to different products through the barometer. The adjustment range is 0~2mm and the adjustment precision is 0.05mm.
16. The waste is automatically collected after die cutting, and the coils are collected neatly.
Equipped with:
Controlling system :Keyence PLC +PC
Servo system :Mitsubishi motors Japan
Suction machine : China-made
Cylinder :SMC
Lead screw :HIWIN
Guide strip slide:HIWIN
The power supply :MEANWELL
Solenoid valve :SMC
Vacuum generator :SMC
Vacuum pump :SMC
Tension control :China-made /Imports optional
Geared motor :Import
Ultrasonic Correction System :China-made /Imports optional
Gluing system :China-made /Imports optional
Technical Parameter:
Overall Dimension :About L4820*W1230*H2200 m
Weight :About 2500kg
Power Supply :AC380V 50/60HZ 70A
Power:35KW
Air Pressure :6KG/CM²
Air consumption:300L/MIN
Control :PC
Outer Diameter of Core : Max. 600mm
Inner Diameter of Core :76mm
Bonding Accuracy :±0.02~0.03mm
Applicable Material :Different sizes of dry Inlay or wet Inlay
Width of Material :20mm---180mm width
UPH :60----90M/Min
Pass Rate :99.9%
Related Keywords