
4 axis cnc milling machines
- Delivery Time:
- 3 Days
Quantity:
Your message must be between 20 to 2000 characters
Contact NowBasic Info
Basic Info
Place of Origin: | Guangdong, China (Mainland) |
---|
Product Description
Product Description
mini 4 Axis CNC milling controller/cnc system Product Description SZGH-CNC1000MDcb 3-5 axis CNC milling controller include 3 axis, 4 and 5 axis , it is closed loop CNC controller and able to work with absolutely encoder motor , support PLC , macro and automatic tool exchange and encoder feedback function,specilized in milling machine center, with I/O 32X32,support bus network connection, and absolutely type motor Linear encoder feedback etc, it is high classes and very stronger CNC milling controller.. Feature: 1) 32 bits high performance, low power consumption industrial grade ARM microprocessor. 2) 64MB memory. 3) 32Mb user store room. 4) 640x480 8 inch real colour LCD displayer. 5) Touch screen main and sub panel. 6) High anti-jamming switch power. 7) USB movable U disc copy interface. 8) RS232 interface. 9) Spindle servo speed control/spindle frequency convertion speed control. 10) Manual pulse generator. 11) PLC and macro function 12) English menu, program and interface, full screen edition 13) CNC1000MDc include 3 axis, 4 and 5 axis , 14) closed loop CNC controller and able to work with absolutely encoder motor Application: CNC milling machinery; machining center; milling center; wood working machine; numerically control grinder; MTDC applied to engraving CNC machine. Technical Specifications : 1) System technical parameter controllable axes:X.Y.Z.A.B five axes. linkage axes:Arc 2-3 axes, liner 2-5 axes. pulse equivalent:X.Y.Z.A.B axes:0.001mm. max speed:X.Y.Z.A.B:60000mm/min. cutting speed:1-10000mm/min. min input unit:0.001mm. program size range:± 99999.999. 99 tools management. program codeISO-840 international standard. program coordinate system definitionISO-841. chassis protection complies with regulation of IP43. 2)System function Auto-diagnosis function All around diagnosis of CPU, storer, LCD, I/O interface, parameter status, coordinates, machining program etc. shall execute when the system starts or resets. In operation, it makes real time diagnosis of power, spindle, limit and all I/O interface. Compensation function automatic backlash compensation. tool radius automatic compensation. tool radius automatic offset and sharp angle transition. leading screw pitch error automatic compensation. it can conduct CAD/CAM/CAPP auxiliary programming by using Pc series compatible computer's abundant software resourcesthen transfer the CNC program into the system to machining throughUSB movable U disc copy portRS232 port .Likewise it also can transfer the program from system to PC through communication port. Application: Metal parts processing ( car/steamship metal processing industry ), glass product ( mobile, TV, computer, electrical switch etc,. glass board proceeding ) , wood furniture etc,. processing produce line (lathe, milling, grinder processing etc)
Standard G codes list
Product physical picture: 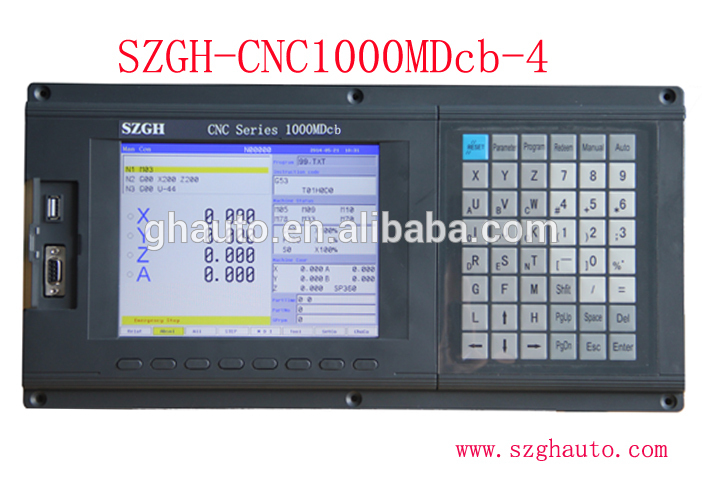
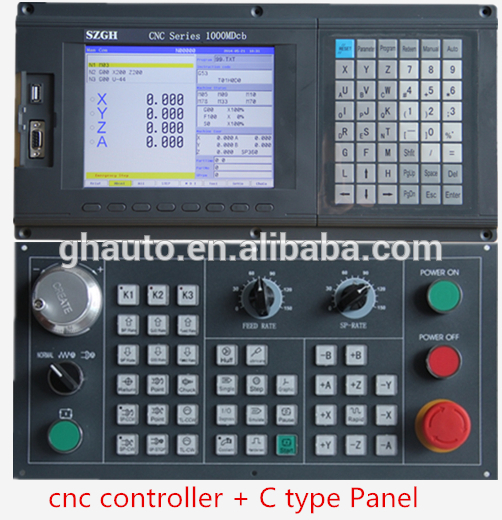
Product Dimension :
Company Information About our company: we can provide with suitable package solution by CNC controller and stepper motor &driver, servo motor & driver, gear box, Shenzhen Guanhong Automation CO.,LTD (short name:SZGH) has professional technical team, strictly product test for high quality guarantee, very competitive quotation, specially we has flexible and convenient payment mode and low cost delivery solution for clients. Our company tenet “Quality is the life of enterprise “, Your satisfy is our greatest achievement. Strictly product manage and test process (high quality guarantee):
Packing detail: 1.Industrial packing: plastic bag +foam boxes+ carton +wooden pallets 2.Commercial packing: plastic bag+ foam boxes + carton 3.As the clients' requirement Delivery Detail: Normally ready goods and stock within 2-5days
Company Information About our company: Website in Alibaba: http://ghauto.en.alibaba.com/ Official Website: http://www.szghauto.com/ Shenzhen Guanhong Automation CO.,LTD (Formerly known as 'Shenzhen Guanhong Automation Technology Co.,Limited(Built in 19 November 2010)') is one of the leading CNC & automatic company in China, specialized in designing projects, marketing, and oversea trading, having extensive experience in CNC package solution, Our focus has been on providing the high quality of Lathe CNC system, Milling CNC system, Engraving CNC system, AC servo motor & driver, TECO servo motor&driver, Stepper motor & driver, Closed stepper motor &driver, Gear reducer. We has professional technical team, strictly product test for high quality guarantee, very competitive quotation, specially we has flexible and convenient payment mode and low cost delivery solution for clients. Our company tenet “Quality is the life of enterprise “, Your satisfy is our greatest achievement. 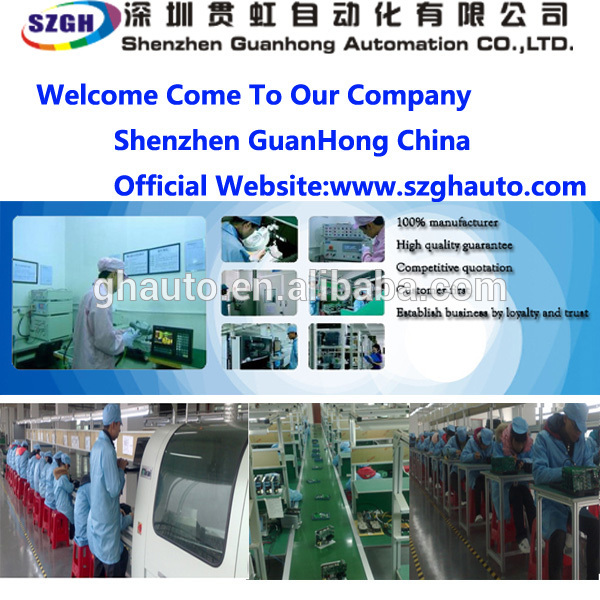
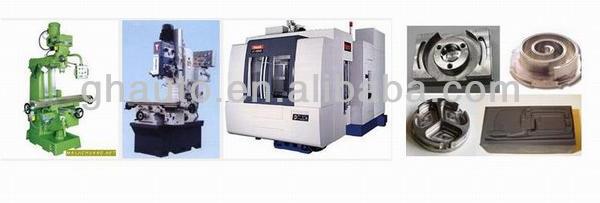
G code | groups | function | ||
G00 | 01 | Fast decides | ||
G01 | The straight line inserts makes up | |||
G02 | Inserts along the circle makes up/the spiral line to insert makes up CW: The spiral motion spiral line inserts makes up the 2 circular arcs insert makes up the axis synchronization migration other axes. The instruction method only is simply adds on is not the circular arc inserts makes up the axis the shifting shaft | |||
G03 | The counter circle inserts makes up/the spiral line to insert makes up CCW | |||
G04 | 00 | pause | ||
G15 | 17 | Polar coordinate instruction cancellation | ||
G16 | Polar coordinate instruction: The polar coordinate (radius and angle), the angle to is chooses the plane the first axis to anti-clockwise changes, but the negative direction is clockwise changes . Form : G** G## G16 G00 IP G Expresses the plane chosen G## mean G90 Work piece coordinate system original point G91 Current position Assigns the polar coordinate and zero point | |||
G17 | 02 | Choose the X Yplane | X axis or its parallel axis Y Y axis or its parallel axis Z Z axis or its parallel axis | |
G18 | Choose the Z X plane | |||
G19 | Choose the Y Z plane | |||
G20 | 06 | Inch input | ||
G21 | Millimetre input | |||
G28/G281/G282/G283/G284 | 00 | Go to first reference point | ||
G30/G301/G302/G303/G304 | Go to 2,3,4 reference point | |||
G26 | ZXY axis go to program original point | |||
G261 | X axis go to program original point | |||
G262 | Y axis go to program original point | |||
G263 | Z axis go to program original point | |||
G264 | A axis go to program original point | |||
G265 | B axis go to program original point | |||
G40 | 07 | Cancel tool radius compensate | ||
G41 | tool radius compensate left | |||
G42 | tool radius compensate right | |||
G43 | 08 | Tool lenthen positive compensate | ||
G44 | Tool lenthen negative compensate | |||
G45 | 00 | Tool adding offset | ||
G46 | Tool subtact offset | |||
G47 | Tool adding two multiple offset | |||
G48 | Tool subtact two multiple offset | |||
G49 | 08 | Cancel tool lengthen compensate | ||
G37 | 11 | Cancel scale zoom | ||
G36 | Enable scale zoom format G36 X_Y_Z_R_ | |||
G12 | 22 | Cancel programmer mirror | ||
G11 | Enable programmer mirror | |||
G52 | 00 | Set local coordinate | ||
G53 | 14 | Chocie coordinate | ||
G54 | Chocie work coordinate 1 | Note These six work coordinate save in CNC user may choice any one | ||
G55 | Chocie work coordinate 2 | |||
G56 | Chocie work coordinate 3 | |||
G57 | Chocie work coordinate 4 | |||
G58 | Chocie work coordinate 5 | |||
G59 | Chocie work coordinate 6 | |||
G60 | 15 | exactitude stop | ||
G64 | Continue path work | |||
G68 | 16 | rotate coordinate format G17 G18 G68 a-b- R-; R:Angle G19 | ||
G69 | Cancel rotate coordinate | |||
G73 | 09 | Drill deep hole cycle format G73 X-Y-Z-R-Q-F- L - Z distance from R to hole bottom R distance from original to R Q feed depth every time F feed speed L repeat time | ||
G74 | Left Tap cycle format G74X-Y-Z-R-P-F- L - | |||
G80 | Cancel cycle mode | |||
G81 | Drill cycle format G81 X-Y-Z-R-F- L - | |||
G82 | Drill cycle format G82 X-Y-Z-R-P-F- L - | |||
G83 | Drill cycle format G83 X-Y-Z-R-Q-F- L -P- | |||
G84 | Right Tap cycle format G84 X-Y-Z-R-P-F- L - | |||
G85 | Drill cycle format G85 X-Y-Z-R-F- L - | |||
G86 | Drill cycle format G86 X-Y-Z-R-F- L - | |||
G89 | Drill cycle G89 X-Y-Z-R-P-F-L- | |||
G90 | 03 | Absolute program | ||
G91 | Increase program | |||
G98 | 10 | Go back to origorinal point |
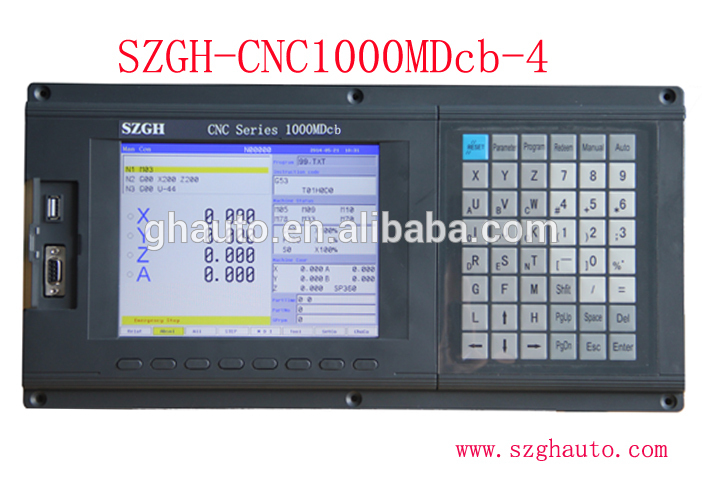
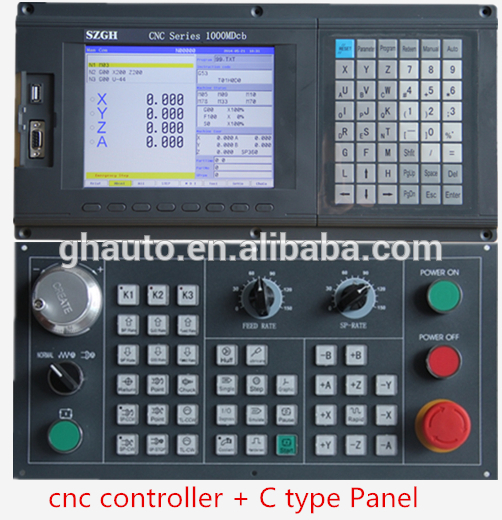
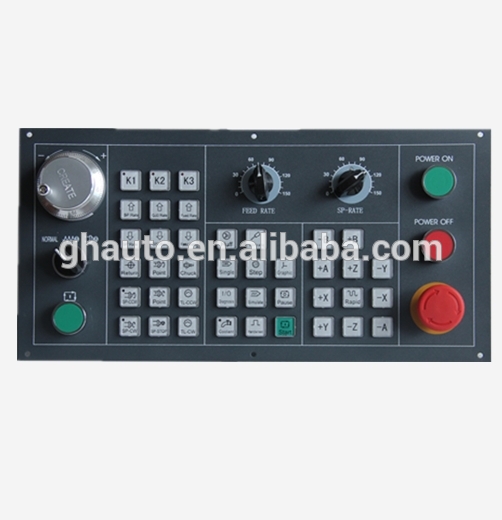
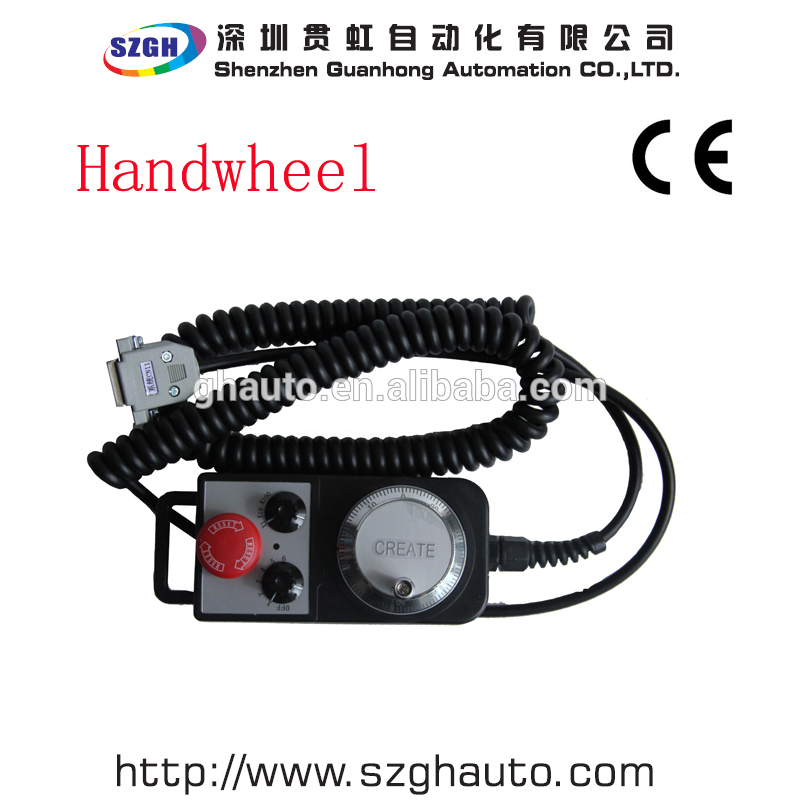
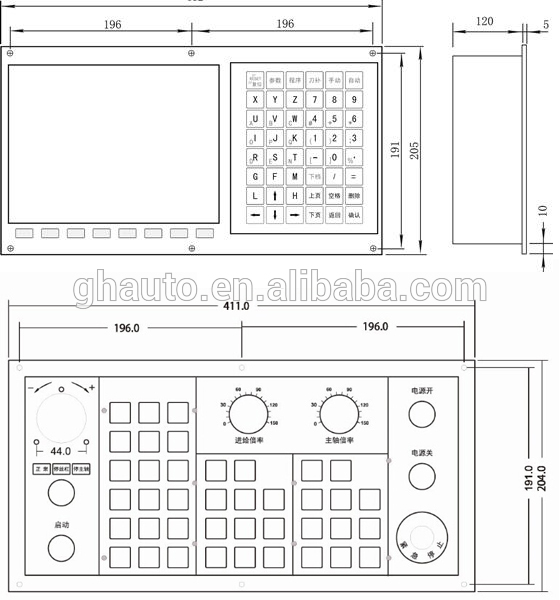
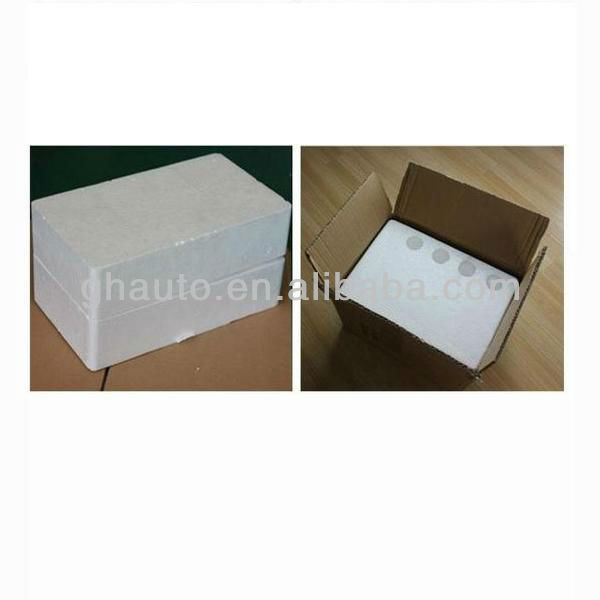
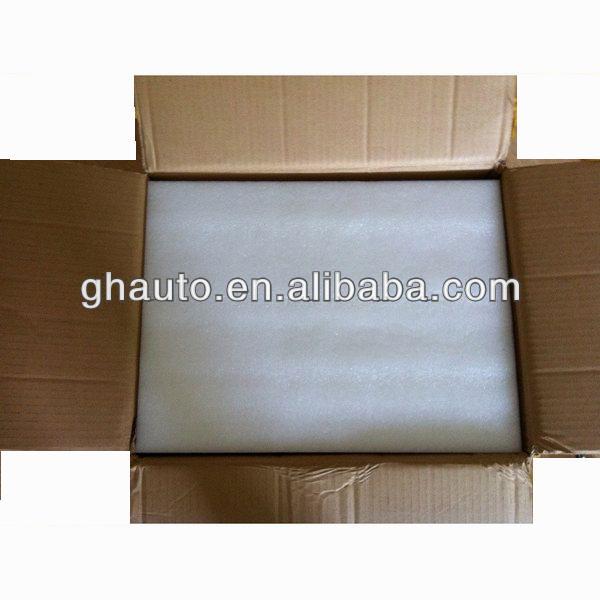
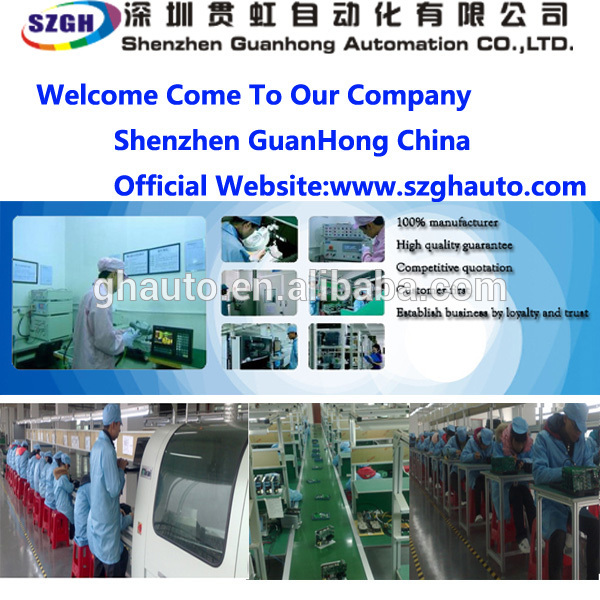
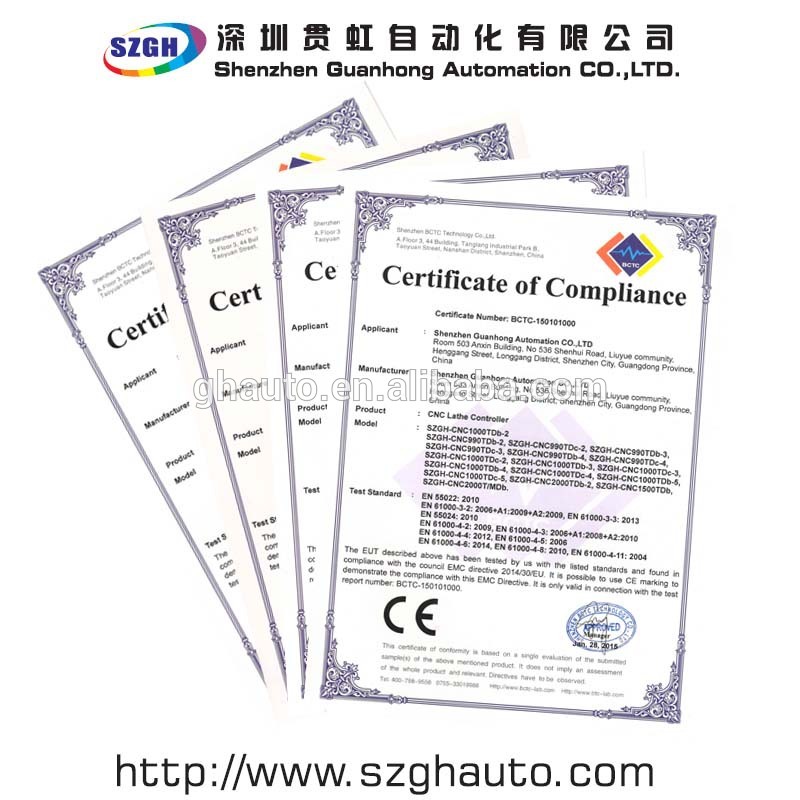
Related Keywords
Related Keywords