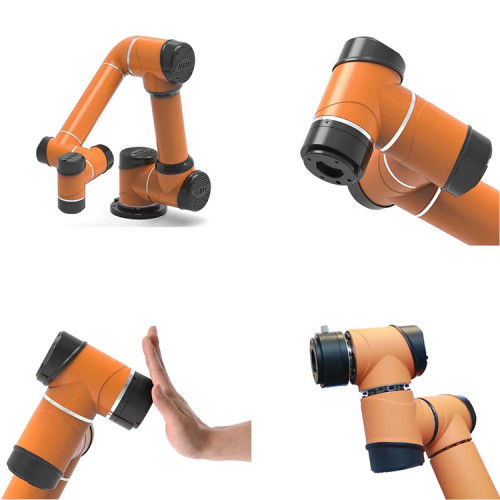
Kingsom Collaborative mobile industrial manipulator
- Payment Type:
- L/C, T/T, Paypal, Western Union
- Incoterm:
- FOB, EXW
- Min. Order:
- 1 Piece/Pieces
- Min. Order:
- 1 Piece/Pieces
- Delivery Time:
- 7 Days
- Transportation:
- Ocean
- Port:
- Shenzhen Port
Your message must be between 20 to 2000 characters
Contact NowPlace of Origin: | Shenzhen |
---|---|
Productivity: | 10000sets/year |
Supply Ability: | Strong |
Payment Type: | L/C,T/T,Paypal,Western Union |
Incoterm: | FOB,EXW |
Certificate: | CE,CCC,ROHS and ISO9001:2008 |
Transportation: | Ocean |
Port: | Shenzhen Port |
Kingsom Collaborative mobile industrial manipulator
The forging manipulator is an automatic device that imitates part of the human hand movement and completes the functions of loading and unloading, transfer between stations according to preset procedures, tracks or other requirements. The use of manipulators in production can ensure product quality, improve labor productivity, free workers from heavy and repetitive manual labor, and can replace human operations in special environments such as high temperature, high pressure, low temperature and dust.
Collaborative Function:Guide to teach (inverse kinematics motion planning), this manual operation of the robot enables quick and easily program the robot by demonstration without any programming skills.Works side by side with human operator without safety fence, laser or sensors (after a risk assessment is preformed).Teach pendent user interface for programing (forward kinematics) enables online programing and simulation via a touch screen tablet.Lightweight, flexible, easy to re-purpose this robot weighs in under 24Kg
Safety Functions:Designed in accordance with PLd and ISO 10218-1 (5.10.5 power and force limiting) safety requirements and compliant with most all specifications for collaborative robot operation.Power and force limiting design brings robot to a protective stop if limits are exceeded or a collision is detected. Speed and force can be adjusted to fit and optimize any application easily.Sensors imbedded in motor drives provide real-time feedback to prevent dangerous situations.Emergency stop buttons are positioned on teach pendent and control box with a braking distance less than 1mm.
Open Source Architecture:CAN bus network used in this robot for multiple microcontrollers to communicate with each other.ROS (Robot Operating System) is supported though API.Hardware adopts CAN bus protocols with open I/O interface extensions.Easily integrate robot into existing production systems.
Return on investment (ROI):Low cost of ownership, no programming skills needed, and ease of integration into a system all add up to a quick return on your investment the average ROI is 3 to 4 months.Short run, high mix environment job like Lab automation or machine tending are prime examples of industries needing fast redeployment.Floor space is a premium cost at most companies usually more than the equipment. A small foot print, light weight robot will be a huge benefit for any size companies cost of production. Repurpose, redeploy and or reinvent applications with the same robot, change the number of degrees of freedom, joints and tubes are modular making it easy to repair as well as reconfigure.
Intelligence
1. Vision systems can be integrated into controller.
2. Software system based on cloud platform management that realizes remote maintenance, fault diagnosis and online upgrading of firmware.
3. This research robot platform is used widely around the world in corporate research labs and for academic robotics research.
Modular Design
1. Robot can be configured to have between four and seven degrees of freedom to meet user requirement.
2. Joint length can be customized to longer or shorter links.
In addition to the Robot Arm Machine, our company also has many products, such as Soldering Fume Extractor, Solder Paste Dispenser, Pneumatic Hand-held Screw Feeder, Automatic Screw Feeder . If you need these products, you can contact us, we will reply to you as soon as possible.
Technical Specifications
Controlled Axed DoF | 6 axes (J1, J2, J3, J4, J5, J6) J7max |
Reach | 924 mm |
Working Range | 880 mm |
Payload | 5kg |
Weight | 24kg |
Footprint | 172 mm diameter |
Collabortative Operation |
Safety monitored stop, speed and separation monitoring, hand guid operation, power and force limiting design. |
Certifications |
ISO 10218-1:2011, EN 60204-1:2006 +A1:2009 ISO 12100:2010, ISO 13849-1:2008, CE |
Repeatability | ±0.02mm |
Linear Velocity | 2.8 m/s adjustable |
Power Consumption | 200 watts typical application |
Materials | Aluminum, Steel, Plastic |
Ambient Humidity | Normal 75% RH or less without frost, or dew, 85% RH short term |
Ambient Temperature | 0 to 45 degrees Celsius |
IP Classification of Robot | IP 54 |
Programing |
Teach Pendant with user interface, guide to teach, ROS compatibility through an API, Lua, Python. |
Communication | CAN Bus |
Motor Type | Harmonic drive 48 Volt |
Installation Orientation | Any celling, Floor, Wall |
Axis | Working Range | MAximun Speed | Max Joint Moments |
J1 axis rotation base | (+/-)175° | 150°/sec | 207Nm |
J2 axis rotation shoulder | (+/-)175° | 150°/sec | 207Nm |
J3 axis rotation elbow | (+/-)175° | 150°/sec | 207Nm |
J4 axis wrist rotation | (+/-)175° | 180°/sec | 34Nm |
J5 axis wrist swing | (+/-)175° | 180°/sec | 34Nm |
J6 axis wrist rotation | (+/-)175° | 180°/sec | 34Nm |
Dimensions (LxWxH) | 683x220x622 mm | I/O Ports | User I/O | Safety I/O | |
Weight | 20kg | Digital in | 16 | 16 | |
Cabling | 5m | Digital Out | 16 | 16 | |
Colour | Black | Analog in | 4 | - | |
Communication | TCP/IP, Modbus-RTU/TCP | Analog out | 4 | - | |
Power supply | 100-240 VAC, 50-60Hz | Power input | 24 Volts | ||
IP Classification | IP54 | Power output | 3A |
Related Keywords